CASE STUDIES
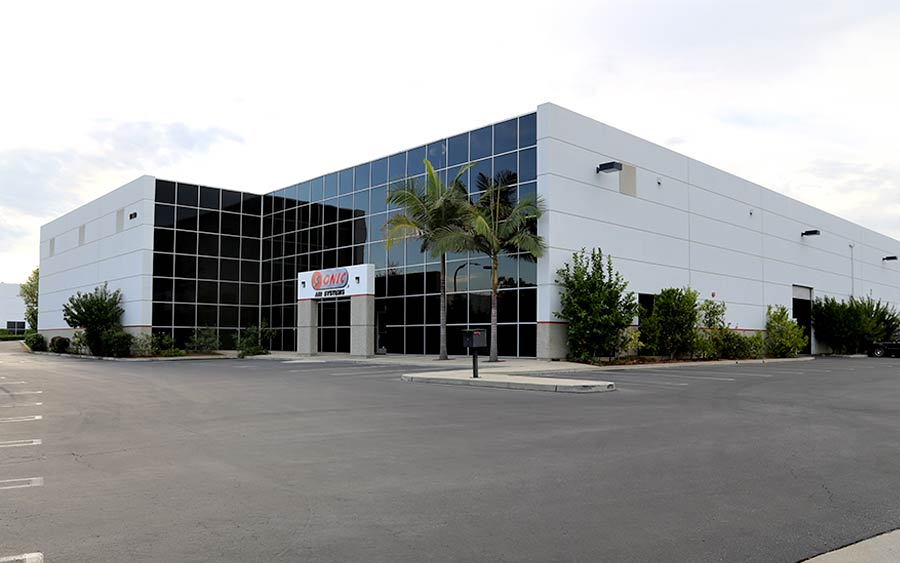
A Game-Changer in Factory Automation
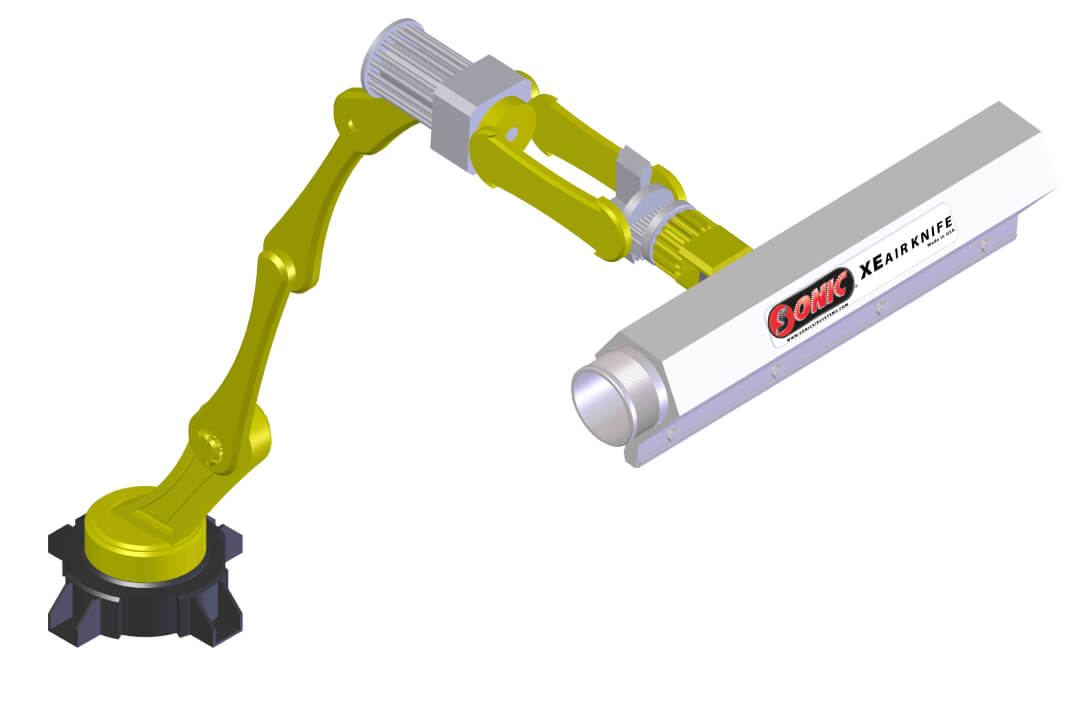
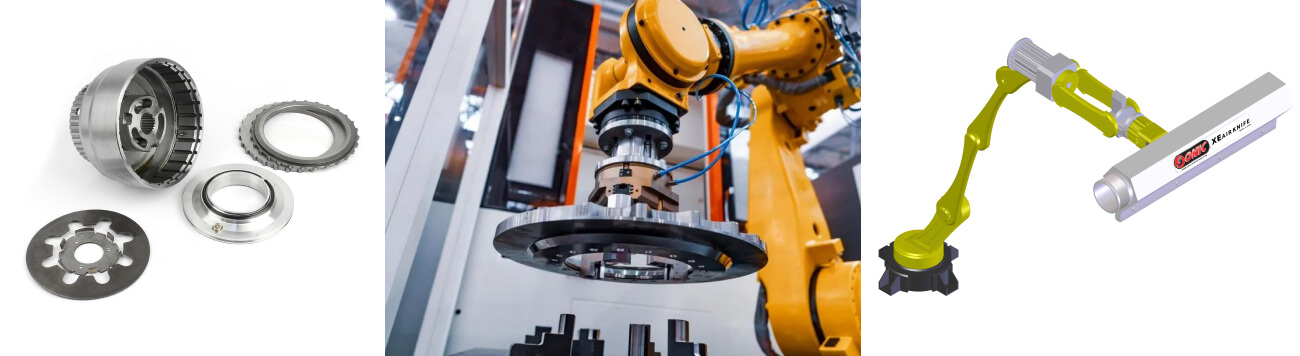
Overview
A Japanese leader in factory automation and a certified integrator of the largest maker of industrial robots in the world required a solution to remove excess machining coolant from the inverted cavity of clutch drum parts before the next machining center process. The excess coolant carryover from one machining center to the next created maintenance issues for the customer. The main objective was to reduce or eliminate coolant carry-over, and equally important was to integrate the Sonic System into the available confined space.
Solution
Sonic's Air Nozzle Manifold Blow-Off system was timed to the "flip" sequence, producing 26,000+ FPM (7,924 MPM) of impact velocity to blow off the inverted cavity while the machined part was stationary for 10 seconds.
Result
Since the installation of the Sonic System, carry-over has been reduced by 90%, resulting in less maintenance of the robotic arm and components while maintaining the small footprint required for the limited installation space.