CASE STUDIES
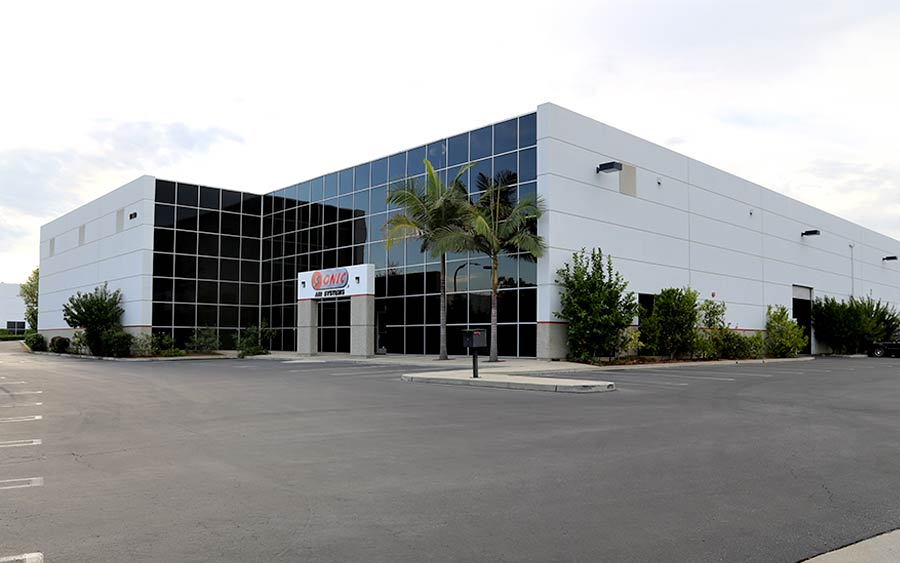
Precision Component Cleaning through the Push & Pull Approach
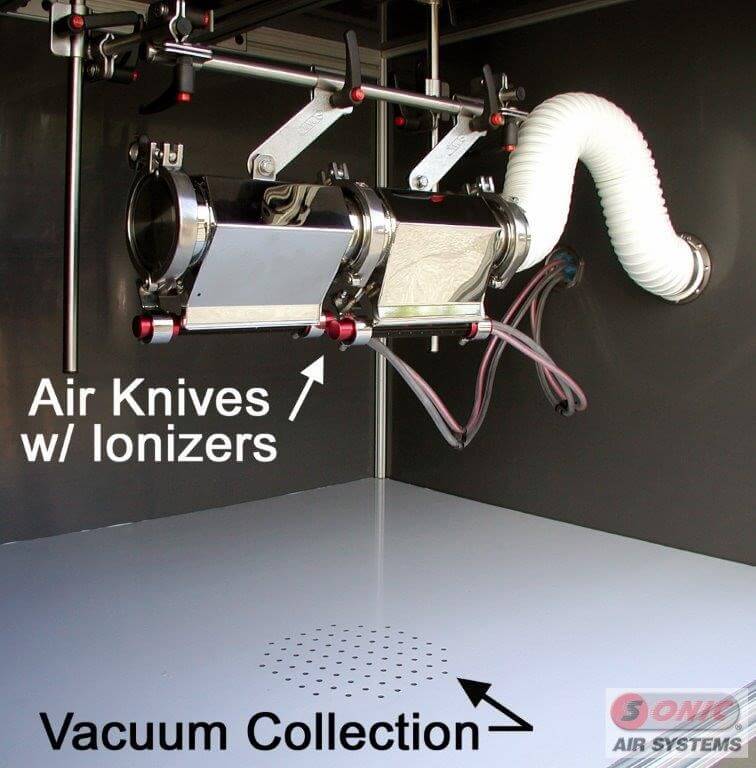
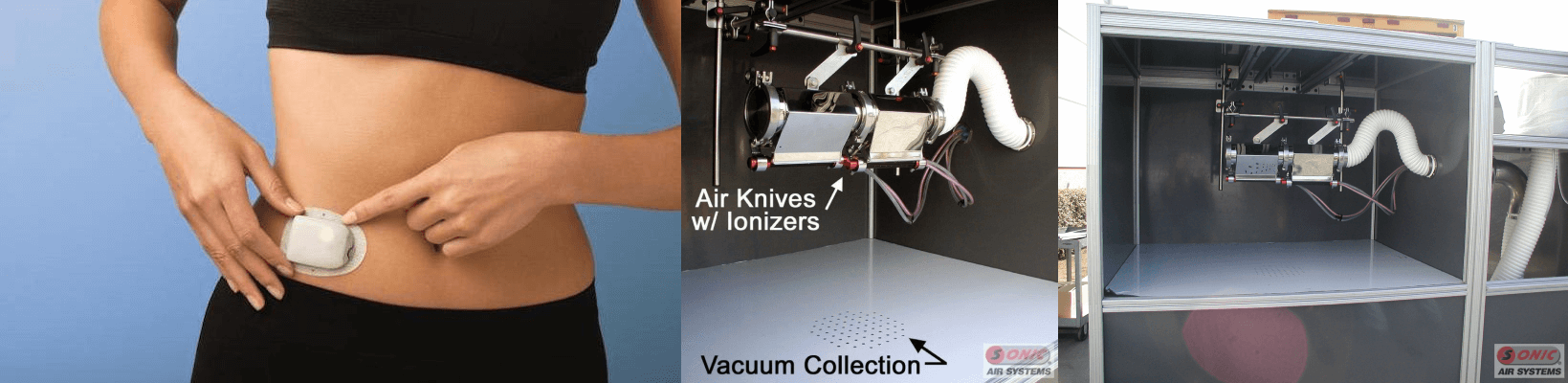
Overview
A major medical device maker was developing a wearable insulin pump and required a Class 100-rated air blow-off system to enhance the cleanliness of some intricate components prior to the pump assembly process. The requirement was to "air wash" their components of any dust or contaminants.
A debris mitigation system is needed to remove microscopic debris from precision screws before inspection. Any microscopic debris will be interpreted as thread damage and then scrapped.
Solution
Sonic designed and implemented a push/pull Air Wash System with Ionized Air Knives powered by Sonic's Centrifugal Blower, mounted within a polycarbonate enclosure. The engineered Sonic Air Wash System "pushes" the air from the blow-off air knives powered by a Sonic Blower while simultaneously "pulling" air from the enclosure to exhaust the discharged air. All equipment is mounted inside a portable Sonic Stainless Steel Blower Enclosure.
Result
The intricate components of the wearable insulin pump are now cleaned of any dust or contaminates prior to the pump assembly process, and the precision screws are now inspected with greater accuracy, preventing misinterpretation of microscopic debris as thread damage and scrapping.