CASE STUDIES
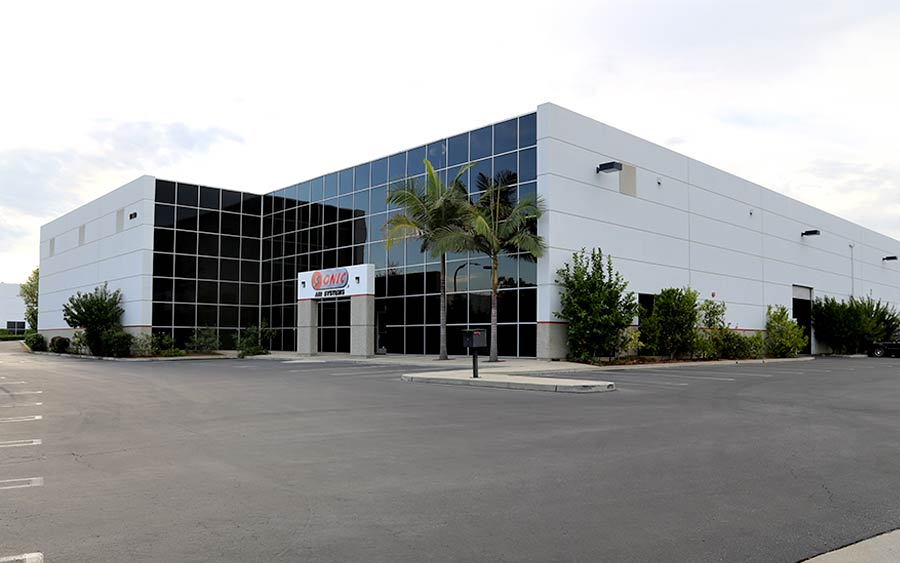
Reduce Costs and Increase Efficiency with Sonic Air Knife System
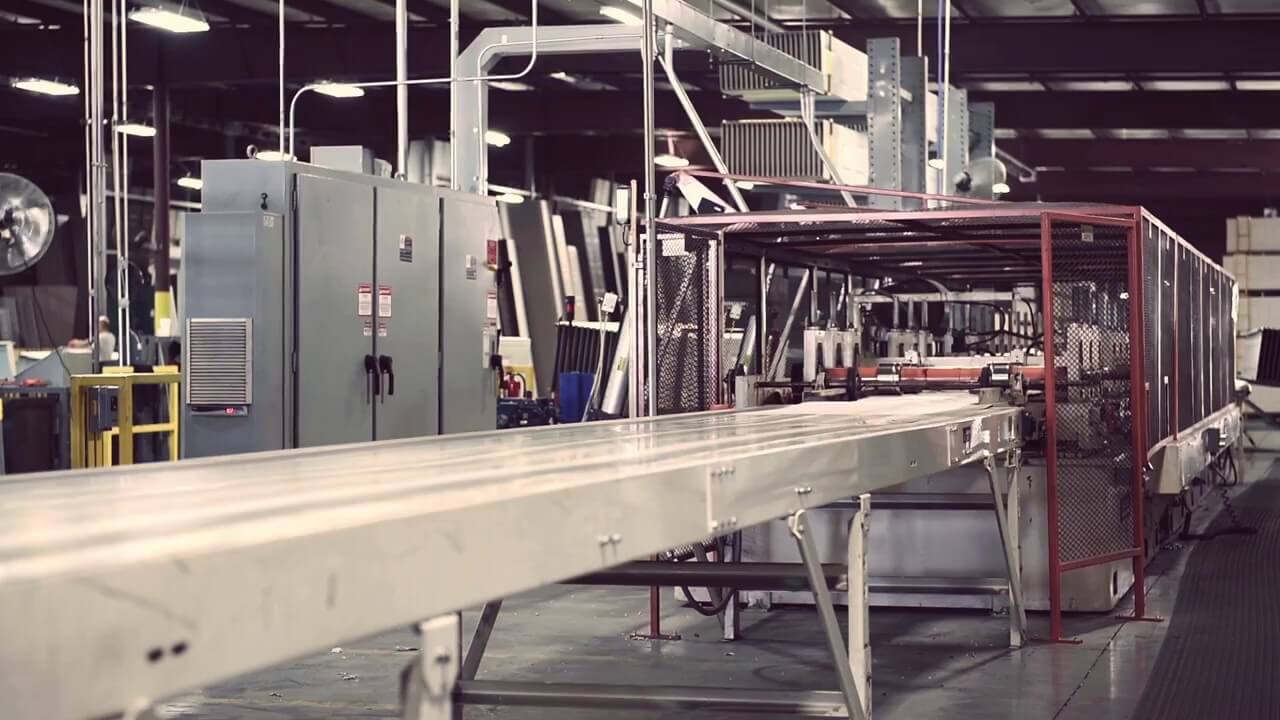
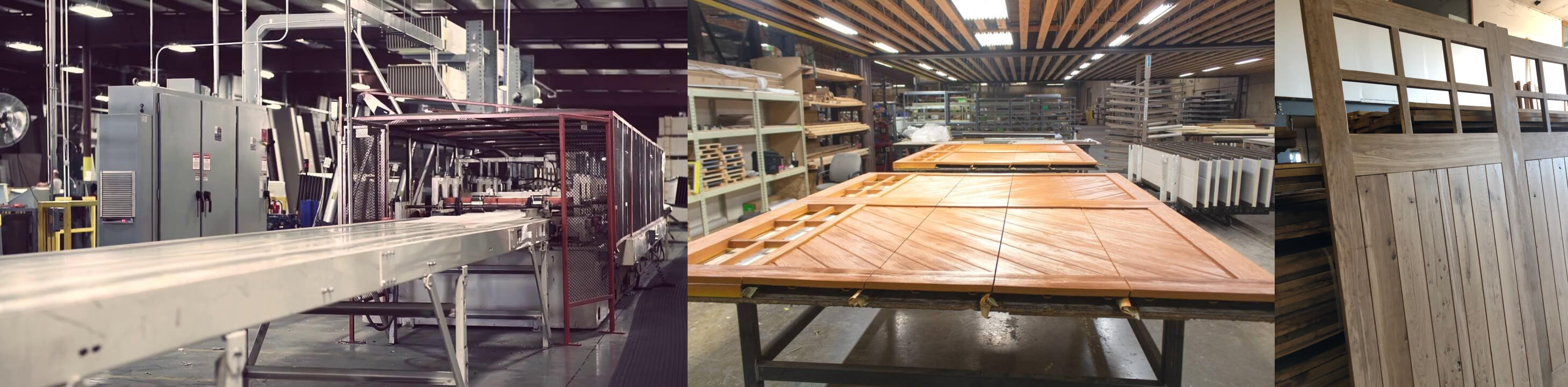
Overview:
Clopay, the largest manufacturer of residential garage doors in North America, needs to remove machined chips from the top of 30” W (762 mm) garage door panels after exiting the “window routing” process. The panels are traveling single file at a production rate of 30 FPM (9 MPM). During this routing process, metal chips and debris need to be removed prior to the next installation process. Clopay had been utilizing a compressed air knife angled across the length of the garage door panel to remove excess debris. However, the compressed air did not provide effective blow-off and required 23.2 HP (17.3 kW) per air knife, equating to $1,800 per shift in annual electricity costs.
Solution
Sonic proposed an Air Knife System that produces 32,000 FPM (9,753 MPM) exit velocities to provide observable impact to remove the excess machining chips to one side, to allow for easy collection and disposal. Sonic's system resulted in an 18HP (13 kW) reduction compared to Clopay's compressed air system.
Result
Once Clopay installed the Sonic Air Knife System, they saw dramatic results. The exit air was more effective at a greater distance and easily pushed the remaining debris across the 30” W (762 mm) panel for collection. Operating costs were reduced by 78.4%, or over $1,400 per shift, annually. As a result, Clopay was able to avoid purchasing a 50HP (37 kW) compressor and reduced the overall load of their current compressed air system.