CASE STUDIES
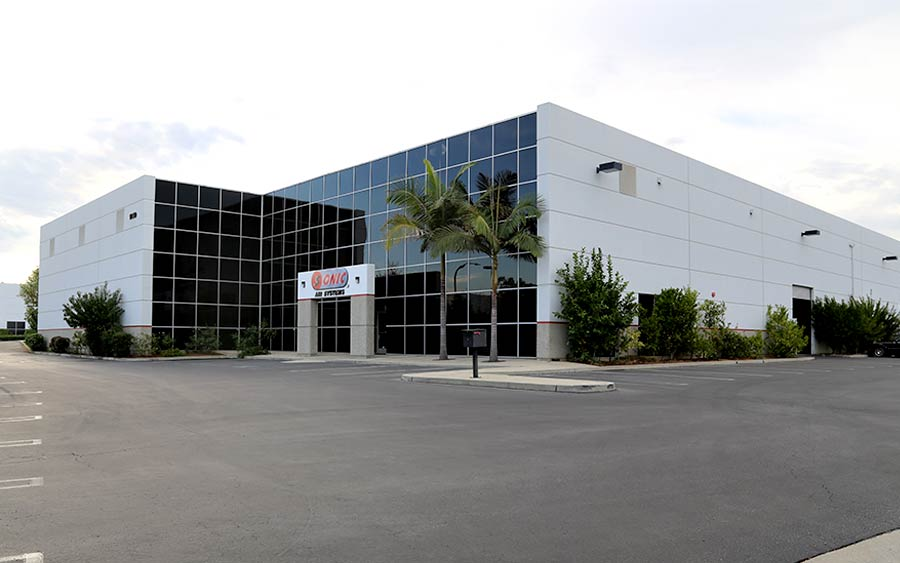
Sonic Air Systems Solution Improves Automotive Paint Line Performance
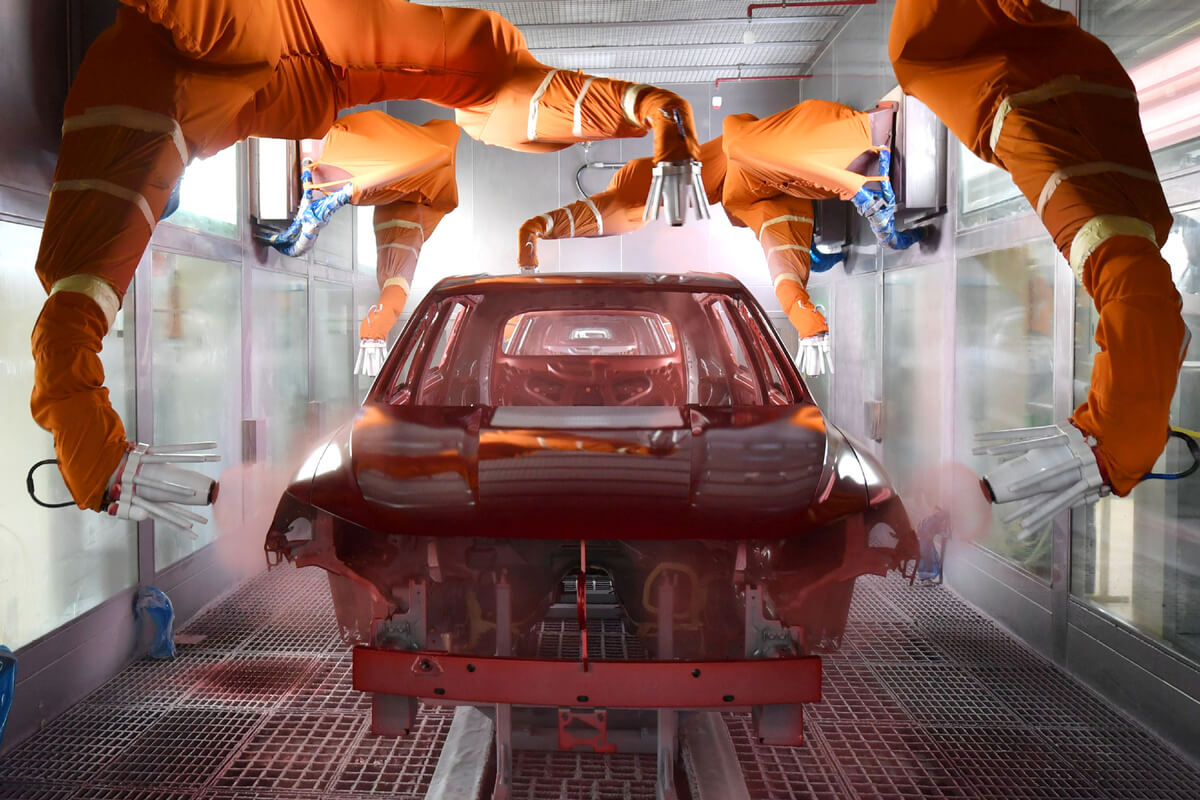
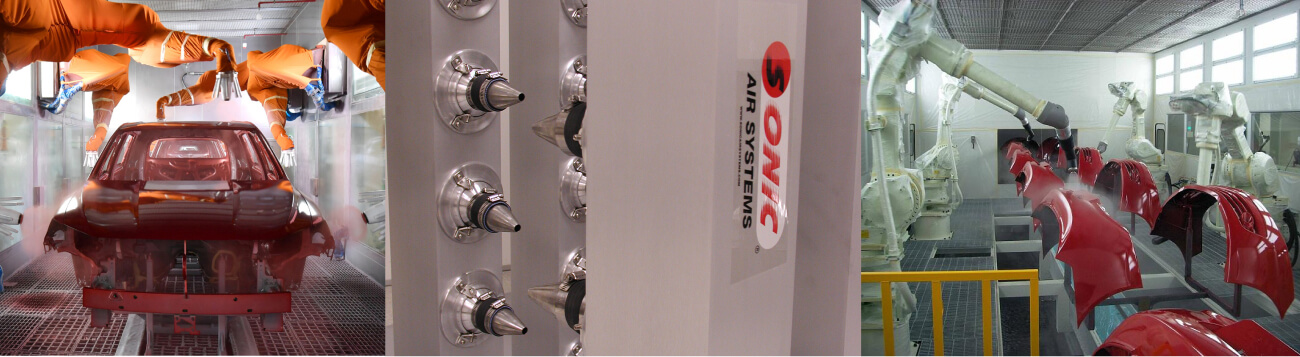
Overview
A major Japanese automotive component manufacturer faced difficulty achieving moisture-free bumper parts after water rinsing. Before they enter the painting tunnel, the complex bumper parts with various features require effective drying to eliminate excess rinse water and improve production quality.
Solution
Sonic Air Systems implemented an advanced Air Knife and Air Nozzle system for drying the bumper parts. The design includes Sonic's XE Air Knives, Swivel Air Nozzle, and Manifolds, effectively removing over 95% of rinse water from all part surfaces and ensuring optimal drying before entering the pre-paint heating tunnel. The solution maximized blow-off effectiveness while minimizing energy consumption.
Result
Sonic Air Systems’ drying solution significantly improved the automotive paint line's performance. The customer reduced oven heating capacity by over 50%, achieving excellent drying results and pre-heating the parts. Ultimately led to a reduction in part rejects caused by excess rinse water and improved the overall operating efficiency of the paint line.