Air Control and Diverter Valves
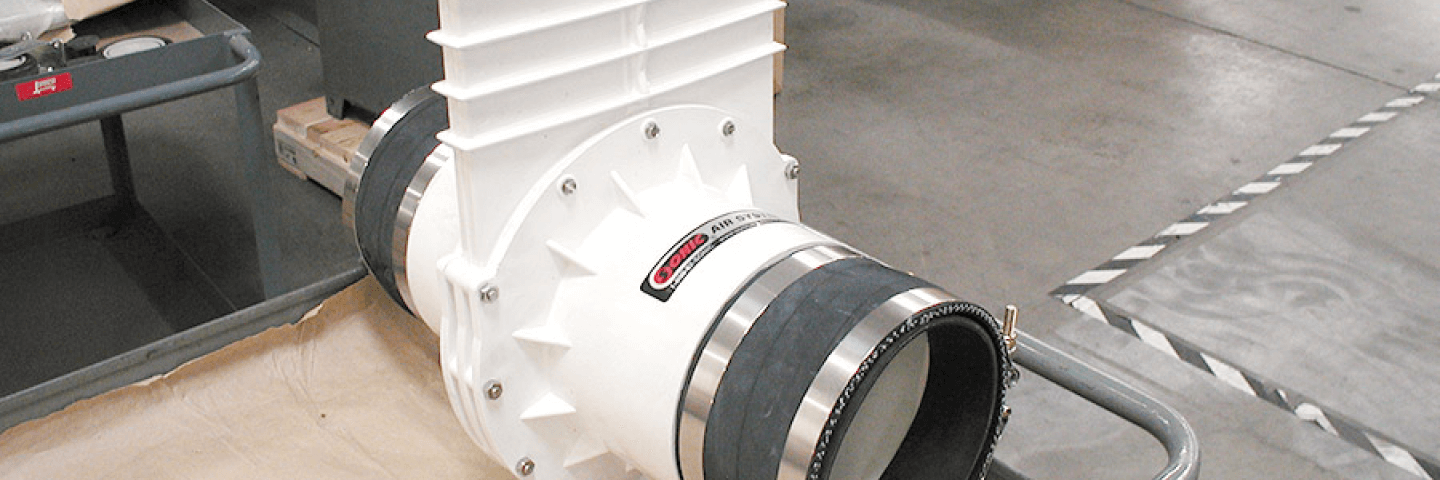
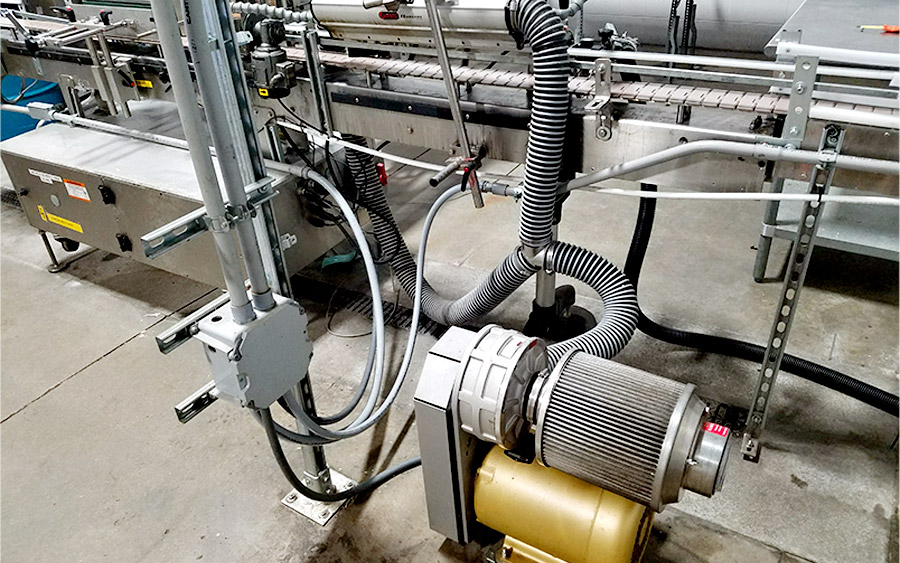
A Smarter Way to Redirect and Regulate Airflow
Sonic Air Systems’ Air Control and Diverter Valves are engineered mechanical components that enable dynamic airflow management without the complexity of electronic variable frequency drives (VFDs). These diverter valves serve a critical function in industrial blower systems by allowing operators to either manually fine-tune airflow or automatically divert it between multiple paths, all while the blower continues to operate at full efficiency.
This is particularly important in high-demand manufacturing environments where precision, uptime, and energy conservation are non-negotiable. Rather than modulating motor speed (as VFDs do), these air diverter valves control air output directly at the system level, reducing wear on motors, avoiding electrical harmonics, and enabling fast response to system demands.
Energy-Efficient Air Control and Diverter Valves
Alternative options to VFD motor controls to optimize operating costs
Sonic butterfly valves can be used in conjunction with a VFD for blower speed control, but our valves can be the only airflow device as they are a low-cost alternative to a VFD. The butterfly valves will allow air knife velocity adjustments to be set to an optimum level during the initial Sonic system installation. The butterfly valve enables the operator to manually adjust the airflow to the desired amount without the expense of a VFD to accomplish the same level of air knife control.
The Sonic Y-Verter is an alternative to VFD motor controls commonly used in blower/air knife systems. Variable Frequency Drive motor controllers are mandatory for some blower manufacturers whose motors run up to 20,000 RPM, with a 330 Hz output frequency from the VFD. Even standard 3,600 RPM, 60 Hz motors that are slowed to certain conditions when paired with a VFD also have to consider whether a Y-Verter™ would be a better choice for air knife control.
Precision Airflow Management for Maximum System Control
- Sonic butterfly valves provide full range flow and pressure control without a VFD
- 3” OD & 4” OD models in stock, and 2” OD are made to order
- Lightweight 6061-T6 aluminum bodies and wafers
- SS shafts with low resistance adjustments
- Control handles with E-Z locking thumb screw
- Save about 50% versus the cost of most VFDs
- No electrical harmonics problems or line conditioners
- No special tools, training, or programming
- No excess heat to motor windings
- Blower air response times to solenoid signals in less than 250 milliseconds
- Y-Verter™ pneumatic actuator is rated for 1 million cycles (open/close)
Specification Sheets
Related Products
Air Control and Diverter Valves
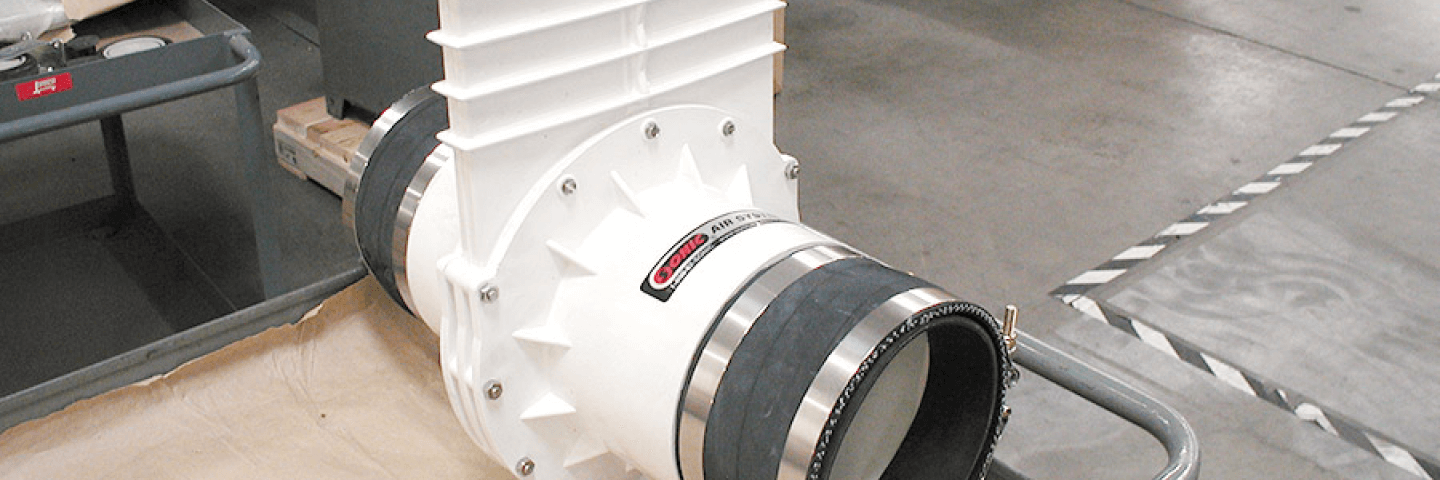
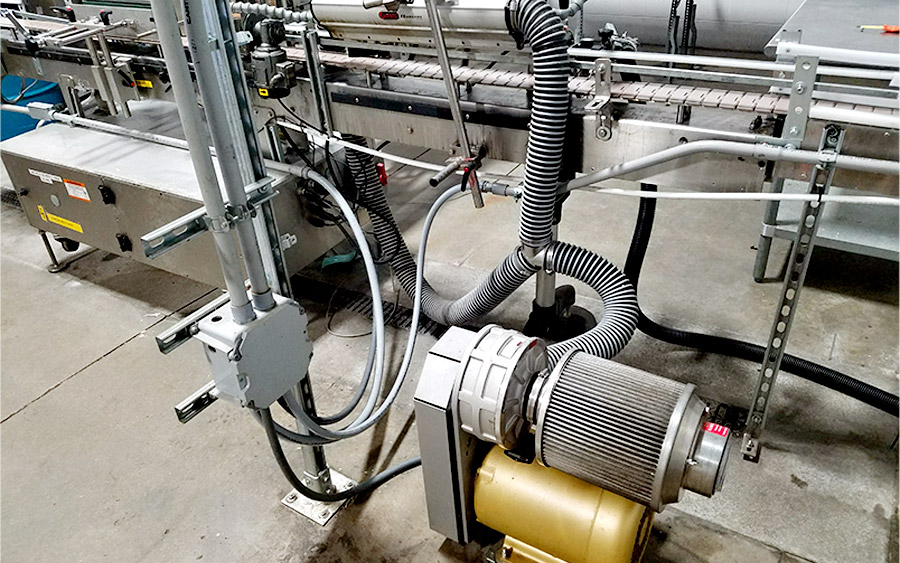
Energy-Efficient Air Control and Diverter Valves
Alternative options to VFD motor controls to optimize operating costs
Sonic butterfly valves can be used in conjunction with a VFD for blower speed control, but our valves can be the only airflow device as they are a low-cost alternative to a VFD. The butterfly valves will allow air knife velocity adjustments to be set to an optimum level during the initial Sonic system installation. The butterfly valve enables the operator to manually adjust the airflow to the desired amount without the expense of a VFD to accomplish the same level of air knife control.
The Sonic Y-Verter is an alternative to VFD motor controls commonly used in blower/air knife systems. Variable Frequency Drive motor controllers are mandatory for some blower manufacturers whose motors run up to 20,000 RPM, with a 330 Hz output frequency from the VFD. Even standard 3,600 RPM, 60 Hz motors that are slowed to certain conditions when paired with a VFD also have to consider whether a Y-Verter™ would be a better choice for air knife control.
A Smarter Way to Redirect and Regulate Airflow
Sonic Air Systems’ Air Control and Diverter Valves are engineered mechanical components that enable dynamic airflow management without the complexity of electronic variable frequency drives (VFDs). These diverter valves serve a critical function in industrial blower systems by allowing operators to either manually fine-tune airflow or automatically divert it between multiple paths, all while the blower continues to operate at full efficiency.
This is particularly important in high-demand manufacturing environments where precision, uptime, and energy conservation are non-negotiable. Rather than modulating motor speed (as VFDs do), these air diverter valves control air output directly at the system level, reducing wear on motors, avoiding electrical harmonics, and enabling fast response to system demands.
Air Control and Diverter Valves
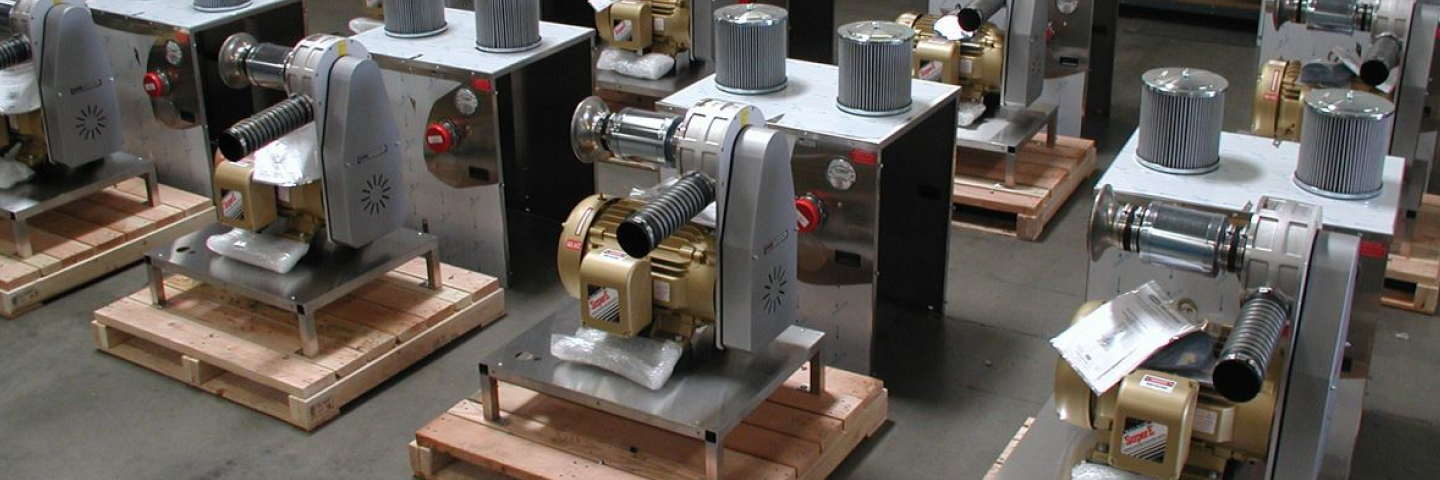
Energy-Efficient Air Control and Diverter Valves
Alternative options to VFD motor controls to optimize operating costs
Sonic butterfly valves can be used in conjunction with a VFD for blower speed control, but our valves can be the only airflow device as they are a low-cost alternative to a VFD. The butterfly valves will allow air knife velocity adjustments to be set to an optimum level during the initial Sonic system installation. The butterfly valve enables the operator to manually adjust the airflow to the desired amount without the expense of a VFD to accomplish the same level of air knife control.
The Sonic Y-Verter is an alternative to VFD motor controls commonly used in blower/air knife systems. Variable Frequency Drive motor controllers are mandatory for some blower manufacturers whose motors run up to 20,000 RPM, with a 330 Hz output frequency from the VFD. Even standard 3,600 RPM, 60 Hz motors that are slowed to certain conditions when paired with a VFD also have to consider whether a Y-Verter™ would be a better choice for air knife control.
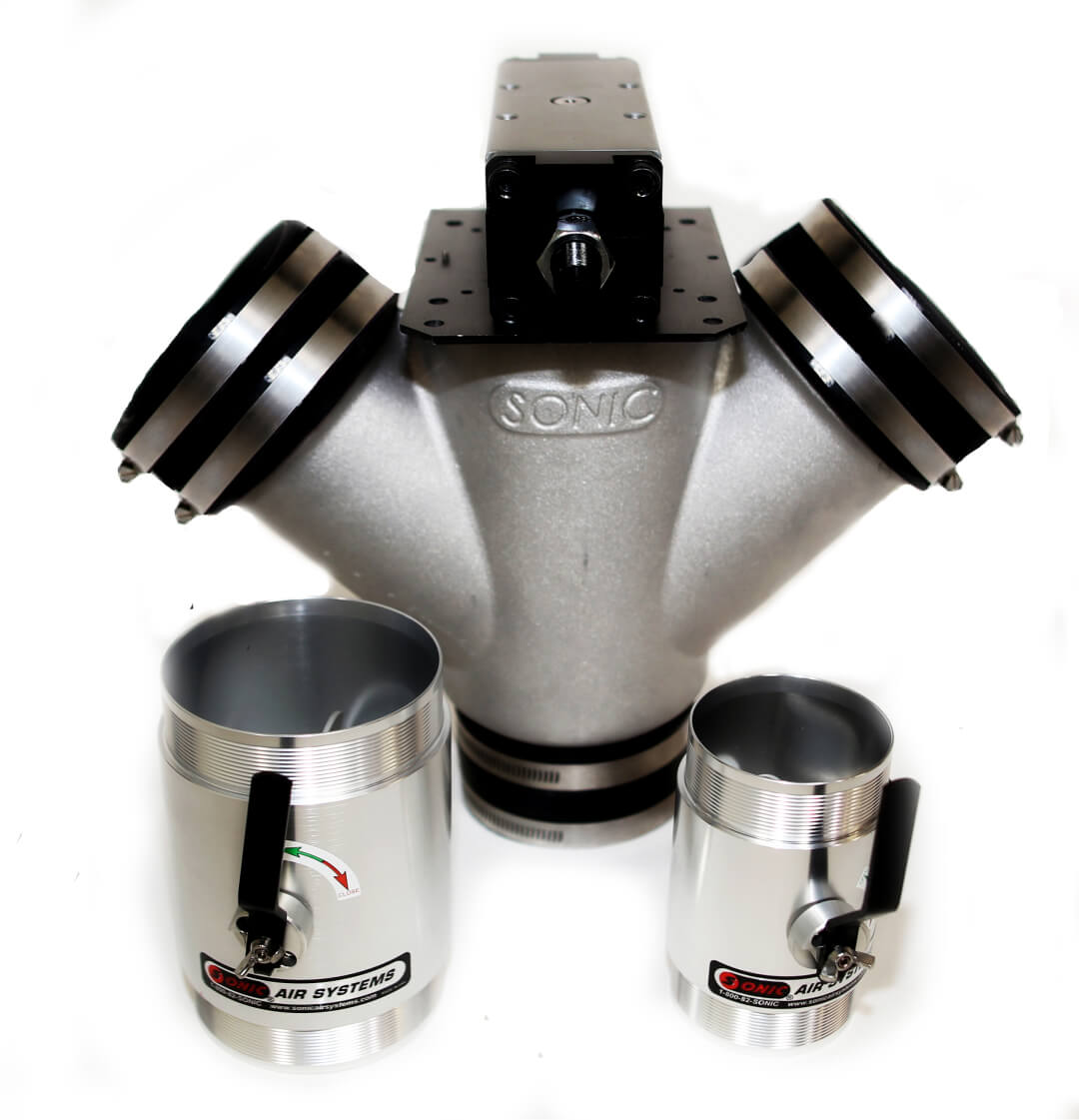
A Smarter Way to Redirect and Regulate Airflow
Sonic Air Systems’ Air Control and Diverter Valves are engineered mechanical components that enable dynamic airflow management without the complexity of electronic variable frequency drives (VFDs). These diverter valves serve a critical function in industrial blower systems by allowing operators to either manually fine-tune airflow or automatically divert it between multiple paths, all while the blower continues to operate at full efficiency.
This is particularly important in high-demand manufacturing environments where precision, uptime, and energy conservation are non-negotiable. Rather than modulating motor speed (as VFDs do), these air diverter valves control air output directly at the system level, reducing wear on motors, avoiding electrical harmonics, and enabling fast response to system demands.