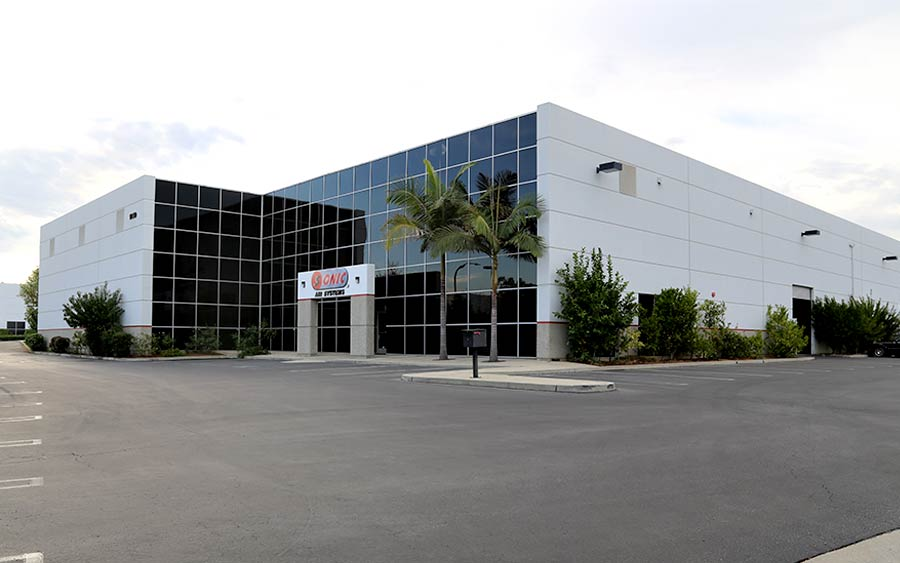
Achieve Precision and Efficiency with the Sonic XE Air Knife Design
%201.png)
Air knives, essential in various industrial processes for efficiently cleaning, drying, or cooling the surfaces of products as they are conveyed through a high-velocity air curtain, have seen significant advancements, particularly after the implementation of environmental regulations like the 1987 Montreal Protocol demanded safer, more sustainable practices.
The 1987 Montreal Protocol and the Shift to Air Knives
The Montreal Protocol marked a significant turning point in global environmental policy. Ratified by nearly 200 countries, it targeted the elimination of ozone layer-depleting chemicals, many of which were used in industrial cleaning and drying processes. Before the treaty, many of the conveyor-driven processes relied on substances like CFCs in their operations. The now-banned chlorofluorocarbons, along with other regulations, have also encouraged significant reductions in the use of other lighter-than-air hydrocarbon-based solvents, coatings, and adhesives used in many manufacturing processes. Most categories of these rapidly evaporating chemicals never required any air knives for drying or blow-off. Although most users understood the personal protective equipment needed to work with them, they didn’t understand the extent of the environmental damage these chemicals could also cause. The worldwide shift towards safer compounds resulted in new chemistries that would perform the same critical industrial functions without the high risk to people and our environment. Industries began aggressively researching alternative, non-evaporating formulas, thereby creating the necessity for more high-velocity air knives.
Although initially powered by compressed air systems, once air knife blow-off devices became a proven complement to the use of all the new mostly water-based chemistries, the pairing of these more environmentally friendly technologies helped meet the objectives of the Montreal Protocol throughout much of our industrialized world. The effectiveness of the traditional compressed air knife methods soon led to the introduction of far more energy-efficient and versatile blower-powered air knife systems to help usher in many new best practices for the 21st century.
The Evolution of Air Knives
The origins of the air knife can be traced to the early 20th century when a few select steel or textile mills needed to blow air out of holes in a small round pipe across a wide narrow area. Today, air knives are an integral part of the majority of conveyor-driven manufacturing in an increasingly diverse range of industries and applications.
Round Tubular Air Knife: Low Manufacturing Cost but with Very Low Efficiencies
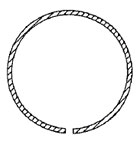
Beginning with the round tubular air knife, its simple geometry originated from high-pressure compressed air and most commonly featured ½” to 1” diameter round pipes having drilled holes along each pipe at ½” to 1” centers. The early low-pressure blower-powered air knife designs continued with round tubes but at 1” to 4” diameter because of the high CFM and with fixed slots machined into them along the length to produce a continuous curtain. The airflow coefficients of discharge for both holes and slots into a pipe or tube is only 0.6 (60% efficiency) resulting in significant exit air pressure loss. The air exiting these sharp-edge orifices also immediately becomes turbulent resulting in the surrounding air excitation and rapid air velocity deterioration for each fraction of an inch away from the orifice exit.
Square Tubular Air Knife: Increased Cross Sectional Area With Tapered Air Exit Efficiency
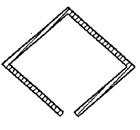
The square tubular air knife was the logical next phase in air knife development. The ready-made structural square tubing allows for the same inlet diameter as a round tube air knife while the increased plenum area of the square corners can accommodate larger air volumes for longer or larger air knife slots. With exit air slots machined into a corner of the tubes, even though the machine's air knife slots still created a sharp edge orifice, the resulting tapered air approach into each exit slot produced flow coefficients up to 0.8 (80%). The exiting air therefore projects out to a greater distance than the round tube before impact air velocities diminish.
Tear Drop Air Knife: Maximize Air Efficiency And Optimize Application Adaptability
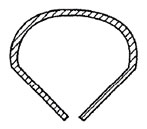
With blow-off air now being applied to conveyor-driven products with more complex geometries, increasingly stringent blow-off standards, and steadily higher production speeds, air knife designs had to improve to keep pace. At the same time, durability, cost-effectiveness, air efficiency, and adaptability to all industries and applications had to be factored into the air knife design evolution. In 1994 Sonic Air Systems invented the industry’s first single-piece teardrop-shaped extruded aluminum air knife profile/plenum engineered to produce a 0.95 coefficient of discharge (95% air efficiency).
Introducing the Sonic XE Air Knife
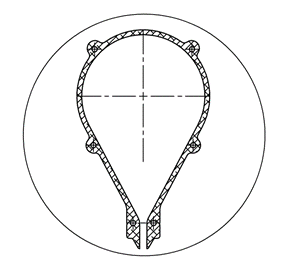
The Sonic XE "eXtra Efficiency" Air Knife development was originally driven by the rapidly expanding personal computer industry, formally the largest single user of CFCs for cleaning printed circuit board assemblies, where Sonic soon became the #1 blower and air knife supplier to the p.c. board industry in the U.S. The Sonic XE Air Knife has ensured that water and water-based chemistries could be effectively removed prior to final board testing for assembly into every type of computerized system today.
As today’s leading blower-powered air knife manufacturer, Sonic Air Systems expanded the XE Air Knife product line to dozens of variations in profile sizes, air nozzle options, materials & coatings, industry-specific design features, and numerous bolt-on accessories to suit every application.
The design of Sonic XE Air Knives & Blower Systems continued to evolve and expand to meet the needs of our worldwide customers. With air knife profiles from 2” to 10,” Sonic offers the XE in hard anodized aluminum, electro-polished stainless steel, and powder-coated steel. As powered by a 3Hp to 50Hp Sonic blower, the XE air knife produces exit air velocities ranging from 10,000 to 40,000 feet per minute (450 MPH) designed by Sonic to deliver the impact air velocity to the products to meet the blow-off objectives for the product the air knife is directed at.
Sonic Features:
- Design Variety: Precision XE Air Knife lengths from 1” to 200” long, slot widths adjustable from 0.010" to 0.250", and nozzle manifolds for air-blowing off products up to 6ft away.
- Energy efficiency: Reduces power consumption by up to 75% compared to even the most efficient compressed air knives or nozzles made today.
- Application Specialists: Blower & Air Knife Systems for blowoff, drying, static neutralizing, coating control, coating drying, product heating with up to 275°F (heater-less) blower air, product cooling with down to 50°F (chilled water) blower air.
- Customization and support: Sonic offers a "performance guarantee" for most blower & air knife systems which we engineer to meet the customer’s specific objectives.
Switch to the Sonic XE Air Knife Today!
The majority of Sonic’s blower and air knife installations are to meet customer needs with ECO-Stewardship benefits for a wide range of applications and industries. As environmental regulations continue to evolve, the Sonic XE Air Knife will remain an integral part of our customer’s production lines and their sustainable manufacturing practices.
For more information on how Sonic Air Systems can tailor solutions to meet your specific needs, contact our team for support or request a quote.