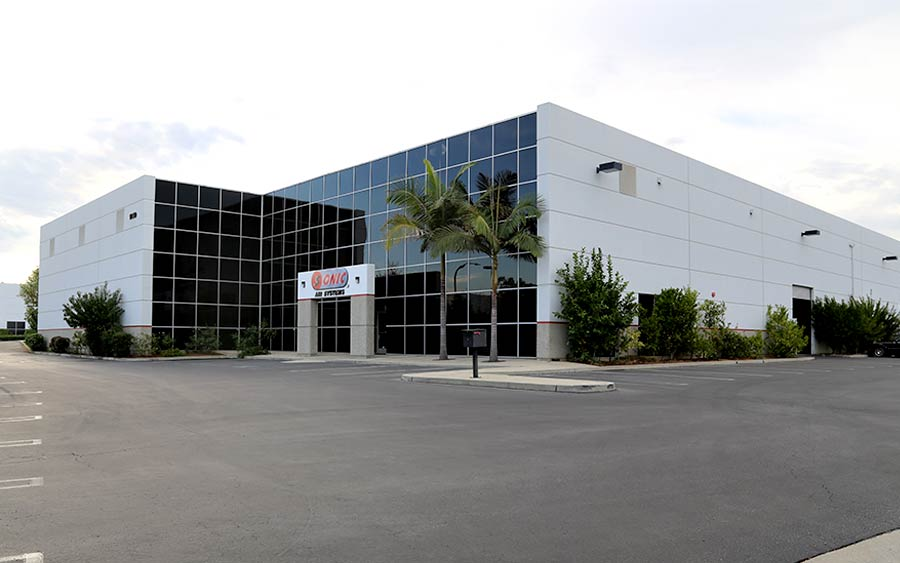
Factors to Consider When You Choose an Air Knife System
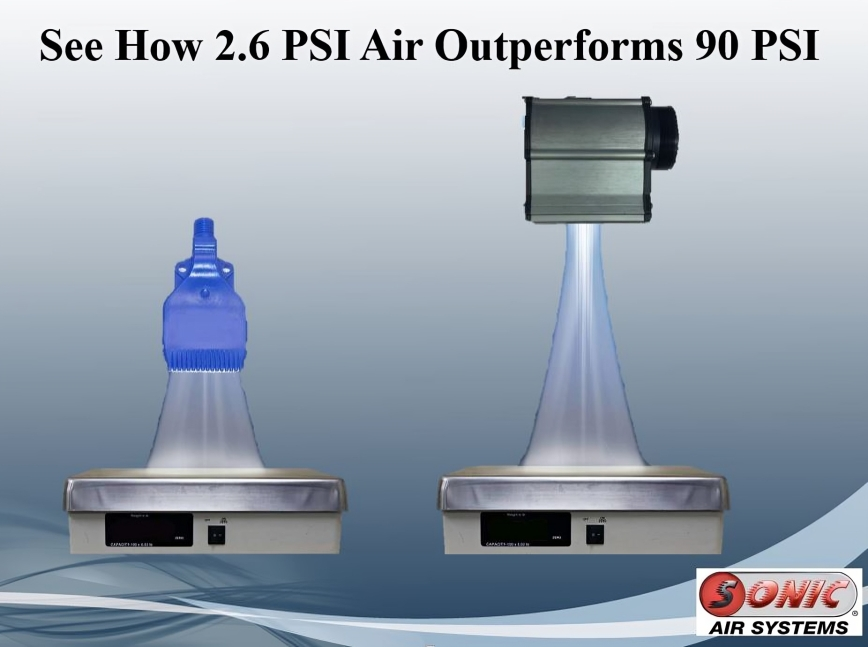
Selecting an air knife system might seem straightforward—find a supplier, pick a model, and get started. However, air knives are not simple, off-the-shelf solutions. Achieving optimal performance and maximizing return on investment (ROI) requires more than selecting from a catalog. With applications ranging from drying and debris removal to coating control and static neutralization, effective and efficient air knife design involves numerous factors that must be carefully considered.
When You Select an Air Knife, It Involves Different Engineering Disciplines
The design and application of air knife systems are not made intentionally complex by manufacturers or experts in airflow engineering. However, creating effective and efficient air knife solutions for today’s wide-ranging industrial applications often involves disciplines like fluid dynamics, thermodynamics, aerodynamics, and material handling.
When faced with a new process requiring a concentrated air blow-off force, users often begin with catalog air knives or nozzles to address immediate needs. These initial solutions allow for pilot line testing or validating a production line’s blow-off requirements. Once these preliminary steps are complete, air knife system specialists can step in to optimize the process and ensure seamless integration into the production line. This is where effectiveness, efficiency, and ROI all come together.
While brute-force air blasting against target surfaces can work, modern advancements in air knife design and application engineering offer significantly better performance. These innovations not only enhance blow-off efficiency but also deliver benefits such as reduced electricity costs, improved product quality, faster production speeds, lower sound levels, and a decreased total cost of ownership.
Key Factors in Air Knife Selection
After categorizing the application and defining the product considerations, it’s equally important to evaluate the part surfaces and the surrounding environment. While some air knife applications are relatively straightforward, making commonly available combinations of air appliances (such as air knives and nozzles) and air movers (blowers and compressors) sufficient, many modern applications require deeper analysis.
As air knife systems expand into industries and applications that were virtually non-existent just a few years ago, the relationship between the target parts and their immediate environment has become increasingly critical. These surrounding influences can impact the performance and design of the blow-off system, as well as its integration with existing equipment and enclosures. This requires a thorough review of factors that may weigh heavily on the system’s success.
Environmental Conditions
- Integration with adjacent systems
- Aerosols or other air flow influences on air knife blow-off function
- Viscosity of fluids to be removed
- Surface tension liquids or charged particles
- Product surface temperature
- Radiation boundary temperature
- Air temperature around the product blow-off area
- Ambient air temperature entering the blower minimum to maximum
- Factory altitude
- Material requirements for air knives and blower
- Blower location from air knives
- Factory sound level requirements
- Electrical standards for factory
Compiling all of the above information then allows for thorough application analysis, although there are still scenarios where varying combinations of information still result in air knife and blower sizing, which relies on empirical outcomes from other applications to arrive at the preferred air knife slot design.
Air Knife Design Considerations
- Coefficient of air discharge: determines the uniformity and efficiency of airflow from the air knife, directly affecting its performance.
- Temperature of discharged air: influences its ability to dry, cool, or treat surfaces effectively, depending on the application.
Optimize Your Air Knife System with the Help of Sonic Air
The reality is that unless someone knows with certainty that a specific air knife sizing, slot design, make, or model will meet all their application criteria, finding detailed guidance can be challenging. Most available information, whether commercial or academic, offers only general product specifications or examples of typical applications. This content often serves as a credential for the company or institution providing it, offering little practical advice on how to design or choose an air knife tailored to specific objectives. While some websites offer performance data such as airflow, air knife velocity, and impact force for various slots or nozzle orifices, users are typically left to rely on trial and error, purchasing an air device to see if it fits their needs.
The largest consumers of air knife systems are the printed circuit board manufacturing and food & beverage industries. These sectors benefit from standardized air knife requirements and widespread deployment of blower-powered systems, allowing for repeatable, optimized drying solutions. However, for other industries and applications, air knife systems must be customized based on unique, application-specific considerations.
An experienced supplier like Sonic Air Systems will help you evaluate your product characteristics, application goals, and environmental conditions to design a tailored solution. If you want our expert advice or are interested in learning more about our products, contact us today to get started.