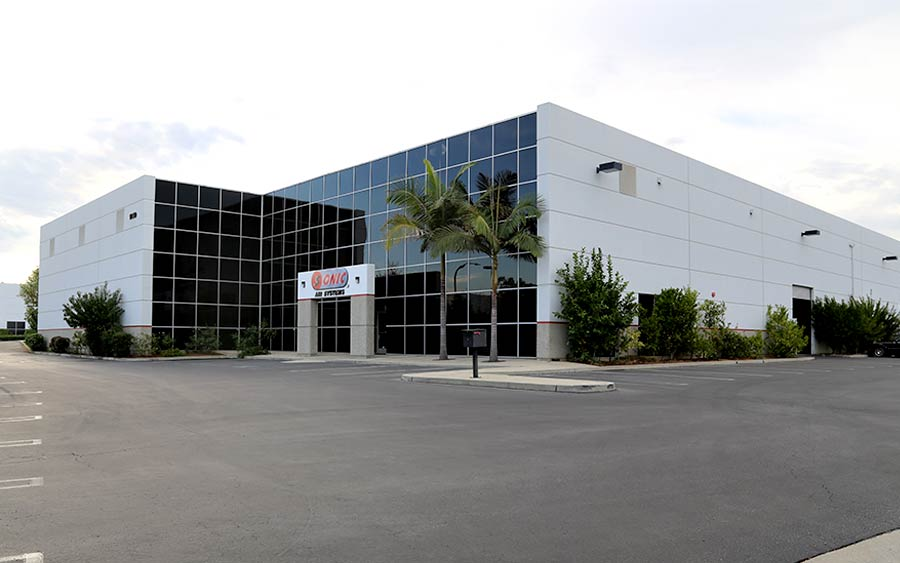
How 2-3 PSI Blowers Meet or Exceed the Air Blow-Off Force of 80-100 PSI
.png)
For many phases of manufacturing in nearly every industry, compressed air systems are such a vital resource that it is often referred to as their 4th utility. Compressed air knives and compressed air nozzles, primarily used for blowing off liquids during manufacturing processes, exploded in popularity in the 1990s after CFCs were banned and the water-based replacement substances didn't evaporate. With the 21st century ushering in the need for even more environmental and energy conservation in all industries, the introduction of blower-powered air knives and air nozzles as a compressed air knife alternative resulted in huge reductions in the power needed for air blow-off systems by 75% versus the former high air pressure blow off devices.
Compressed air for blow-off applications now consumes a much smaller portion of most central plant air systems, but the creation of the new low-cost and widely available injection molded flat jet air nozzles has become the largest-selling compressed air blow-off device worldwide. It represents a quick plug-and-play option for factories until they have determined what size blower-powered system would suit their needs. Even though the 80-100 psi flat jet air nozzles offer improved blow-off force and efficiency versus older blow-off devices, they still require large sums of compressed air together with consuming 4X more electric energy versus air blowers with air knives or air nozzles at 2-3 psi.
When engineers and maintenance people search "How do I choose the right air knife," they quickly learn that the return on investment for the higher initial cost blower powered air knife systems rarely exceeds 12 months, and usually it is much shorter, based solely on energy savings versus compressed air. The age-old saying, "You get what you pay for," has never been a more accurate statement when it comes to choosing a properly sized blower and air knife system.
The Inefficiencies of High-Pressure Air Knife Systems
Although high-pressure compressed air can produce some very high air velocities exiting from air knives or air nozzles, it is not the discharge air velocity that matters but how much of the turbulent air shear (blow off) force is required to impact the target surface to which the air knife is being directed that is most important.
Compressed air systems can have a typical pressure range of 100-150 psi, which, if they have minimal friction losses before exiting a compressed air knife, could produce theoretical discharge air knife velocities up to several times the speed of sound. In practical terms, most compressed air piping and hoses are not large enough in diameter, nor is other compressor system support equipment (dryers, oil separators, receivers, and regulators) usually sized to handle the higher air volumes required by the add-on air knives or nozzles which are so often the result of process changes over time. It is not uncommon to then experience 25-75% air pressure loss before reaching an air knife or nozzle discharge. In those cases where the central plant air piping is sized to deliver the higher air pressure at high CFM all the way to the air knives or nozzles, the exceptionally high exit air velocities that are possible can produce correspondingly high sound levels from those air knives or nozzles. At the same time, the compressor power allocated to successful blow-off force will always average 75% greater than a blower-powered air knife or nozzle system for the same application.
The Science Behind Sonic's Efficient Air Flow Design
When determining who the best air knife companies are, Sonic Air System's 35 years of experience in blower air engineering often makes them a leading choice. Our development of air knife and air nozzle products to suit the endless application variables we have seen to date has allowed us to conduct a thorough analysis of a wide array of compressed air blow-off devices and the compressed air systems that power them. Sonic’s comparative testing of high-pressure air exiting narrow slots or small nozzles at velocities of MACH 1 or higher didn’t outperform Sonic’s impact force unless the 80-100 psi slot or nozzle was <½” from the surface it was blowing on.
Although the flat jet air nozzle is the most popular compressed air device, many users connect multiple flat jet nozzles side by side into header pipe to blow air across large-width conveyors, which makes these nozzles the perfect compressed air device to evaluate head-to-head against Sonic air knives and Sonic air nozzles.
The Testing Parameters
The primary reason that 2-3 psi blower air can discharge at laminar airflow from a Sonic XE Air Knife slot is because we have a properly sized air plenum to reduce internal turbulence and then uniformly accelerate to the maximum exit velocity along the entire orifice or slot length to achieve a 0.95 coefficient of friction (95% efficiency) along with a much larger exit slot width or nozzle diameter thereby delivering a 3-5X higher air volume than compressed air. This same efficiency characteristic is achieved with a variety of air knife and nozzle designs that we offer. Since measuring actual impact shearing force is difficult to quantify from a single air impact point, a head-to-head test of total air downward force onto a weight scale provides a more relevant and representative comparison between 2-3 psi blower air versus 80-100 psi compressed air.
The result, assuming the compressed air devices are achieving the required blow-off force, is that the higher air volume and efficiency of the 2-3 psi air knife or nozzle produces the same impact blow-off force, requiring only 75% less electrical power.
By comparison, even if the required compressed air pressure at the air knife or nozzle could be regulated down, or where significant air pressure pipe losses drop the nozzle pressure to 15-20 psi, with the user being satisfied with that blow-off force and lower CFM, the parasitic losses of generating 100+ psi at the compressor remain. All air compressors require 1 Hp of electrical load to produce every 4 - 4.5 CFM, depending on total system efficiency, so whatever the final nozzle air pressure and CFM, a Sonic air blower will always make the same blow-off force while requiring 75% less energy. There are very few application exceptions to this widely known fact.
Nozzle Testing: Sonic Blower vs. Compressed Air Test
A 6" diameter force scale was placed in front of different nozzle configurations. Measurements were taken at ½" intervals, up to a 6" height from the flat plate of the scale.

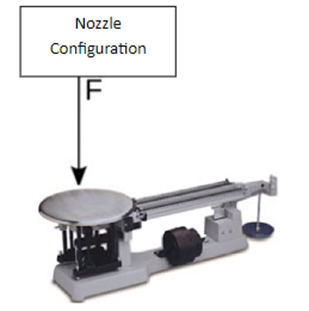
See How 2.6 PSI Air Outperforms 90 PSI
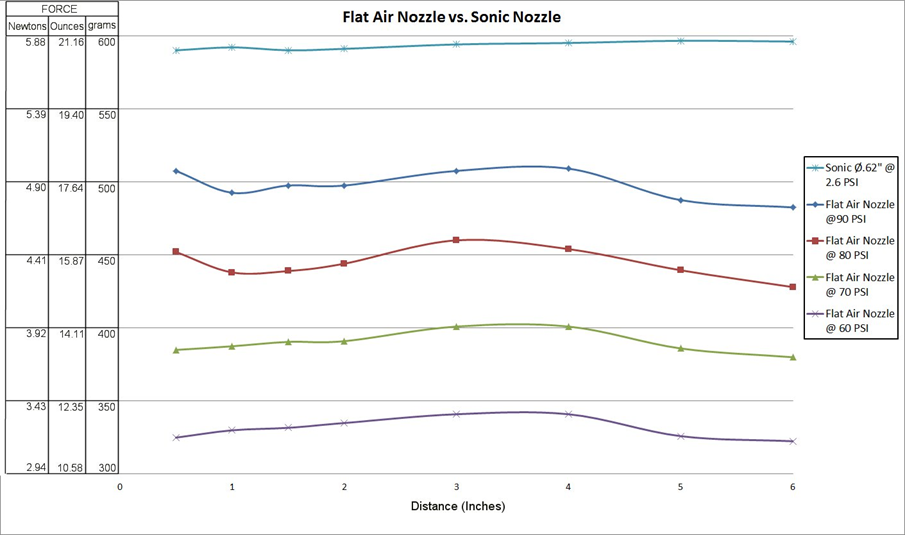
Metrics of Evaluation: Force and Power Force
A Flat Jet Air Nozzle 1-7/8" wide with a ¼" NPT connector achieved the highest force results out of the compressed air nozzle products that were tested. This was compared to a single Sonic Ø.62 Air Nozzle, at max achieved blower pressure of 2.6 PSI.
Power
The Sonic Ø.62" Nozzle operates impressively at a lower pressure of 2.6 PSI, requiring only 1.24 HP per nozzle. This contrasts sharply with the traditional Flat Jet Air Nozzle, which operates at a higher pressure of 90 PSI. The comparison between these two nozzles was strategically chosen because the Flat Air Nozzle produced force results that were closest to those of the Sonic Ø.62" Nozzle, using standard metrics such as mass flow rate, temperature, and pressure to calculate the necessary power for achieving such high pressure.
The efficiency of the Sonic nozzle becomes even more apparent with its ability to throttle down effectively to match the lower force outputs of the Flat Jet Air Nozzle while still achieving substantial energy savings. When the Sonic Ø.62" Nozzle is adjusted down to 2.02 PSI, it achieves an 82% reduction in power usage compared to the high-pressure scenario. Further adjustments to 1.97 PSI to match the force output of a Flat Jet Air Nozzle operating at 80 PSI result in an even more impressive 83% power reduction. These adjustments highlight Sonic's commitment to not only matching but exceeding the performance of traditional high-pressure systems with significantly lower energy consumption.
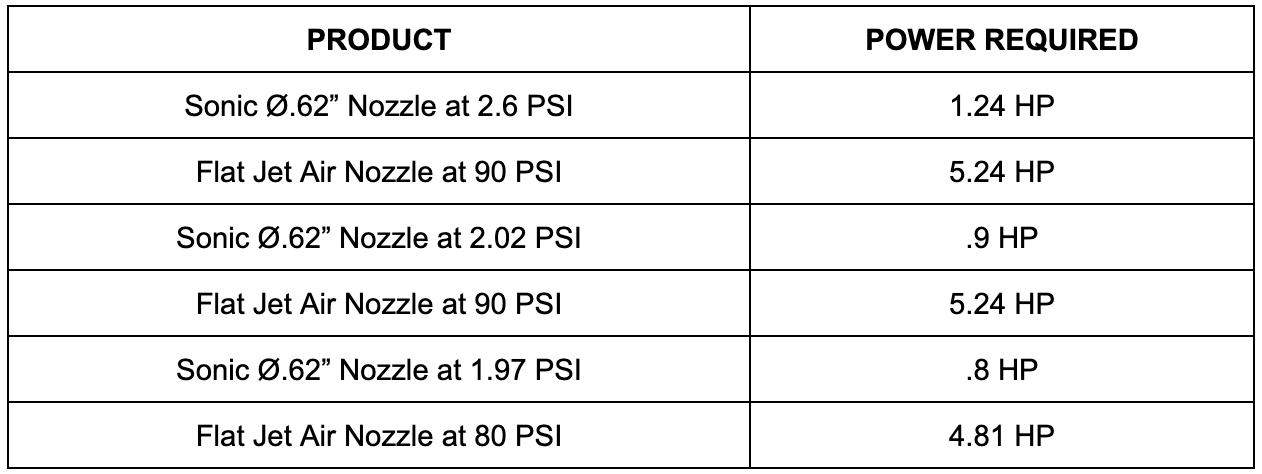
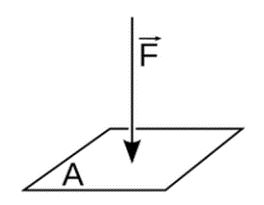
Analysis
Force can be characterized by the equation:
Force = (m)(v)
m = Mass Flow Rate
v = Average Stream Velocity
Simply put, compressed air products operate at higher velocities but at much lower mass flow rates than Sonic Blower Nozzles. The higher flow rates of the Sonic Blower Nozzle make up for lower velocities.
Flat Air Jet Nozzle Compressed Force = (m) (v)
Sonic Blower Nozzle Force = (m)(v)
Continuous operation to provide this increased mass flow rate requires less work than compressing the air to a high pressure and relying on high velocities.
Sonic's blower-powered nozzle generates the same impact velocity as the compressed air-operated nozzle but produces a much more mass flow rate, so it generates greater impact force at lower pressure, using 4-5X less power.
Experience the Sonic Difference Today
The shift towards low-pressure Sonic blower air knife and air nozzle systems is more than just a trend; it represents a fundamental shift in industrial practices toward more sustainable and cost-effective solutions. The evidence clearly supports that these systems not only meet but very often exceed the performance capabilities of traditional high-pressure compressors.
To explore how Sonic Air's innovative solutions can transform your operations, browse our products or contact us directly for more detailed information and tailored solutions.