Air Knife Systems
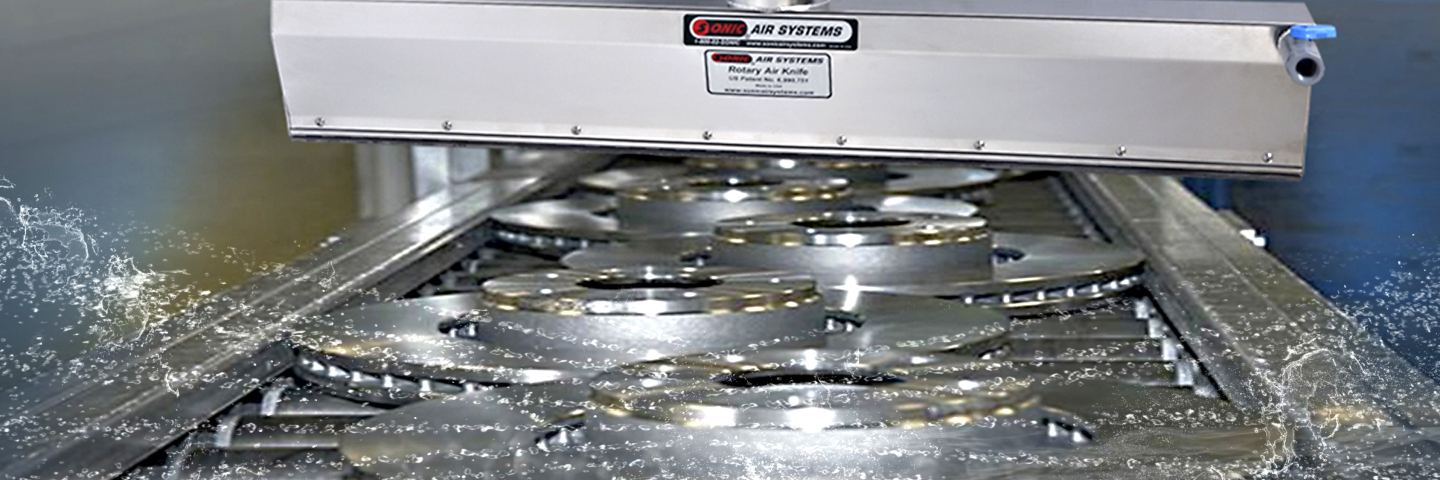
-min.jpg)
Comprehensive Line of Sonic’s Air Knife Systems
Effective drying and blow-off air knife systems for a wide range of industrial applications
Sonic Air Systems is a leading manufacturer of industrial air knife systems designed for a wide range of applications. Our comprehensive line of air knives and accessories caters to diverse industrial environments, providing effective drying and blow-off plus hot air and cold air solutions. Whether for surface preparation, cleaning, or other industrial processes, our air knife systems deliver reliable performance and optimal results.
Our Products
Browse our selection of air knife drying systems, built for consistent performance and durability in challenging industrial environments.
Our Products
Browse our selection of air knife drying systems, built for consistent performance and durability in challenging industrial environments.
Achieve Superior Performance and Optimized Production with Sonic Air Knife Systems
Industrial air knife systems are specialized tools that use a high-velocity, focused air stream for cleaning, drying, heating, or cooling products and surfaces in industrial processes. The system works by forcing pressurized air through a narrow slot, creating a powerful, uniform sheet of air that precisely targets the surface area. This airflow effectively removes moisture, contaminants, and heat from the products or materials being processed.
Sonic’s high-velocity air knife systems are used across many industries, such as food, beverage, automotive, electronics, and steel rolling mills. In the food industry, they are crucial for drying and cleaning products during production, ensuring hygiene and efficiency. In automotive manufacturing, air knives remove excess water or debris from vehicle parts, while in electronics, they dry P.C. boards prior to testing. Their ability to streamline production processes and reduce waste makes Sonic Air Knife Systems indispensable in numerous industrial settings.
.jpg)
Revolutionary Air Knife Technology for Optimal Performance
FEATURES
- Versatile Functionality: Air knife systems designed for various applications, including drying, cleaning, heating, and cooling, to streamline multiple industrial processes with one system.
- Energy Efficiency: Advanced design and engineering reduce energy usage, providing long-term cost savings while maintaining peak performance.
- Flexible Integration: Easily integrates into existing production lines and enhances overall system performance without requiring significant operational changes.
- Precision-Engineered Industrial Air Knife Systems: Manufactured to exacting tolerances, ensuring consistent and uniform airflow for optimal performance.
BENEFITS
- Increased Production Speeds and Throughput: High-velocity airflow efficiently dries, cleans, heats, and cools products, which allows for faster turnaround times and higher production volumes.
- Reduced Downtime: Durability and easy maintenance reduce the frequency of repairs and system downtime, keeping production lines running smoothly.
- Improved Product Quality and Consistency: Precise airflow ensures uniform coverage and improves product quality and consistency with fewer defects or inconsistencies.
- Cost-Effective Operations: By reducing energy use without compromising performance, our systems ensure long-term savings as they lower energy bills and overall operating expenses.
View Case Studies
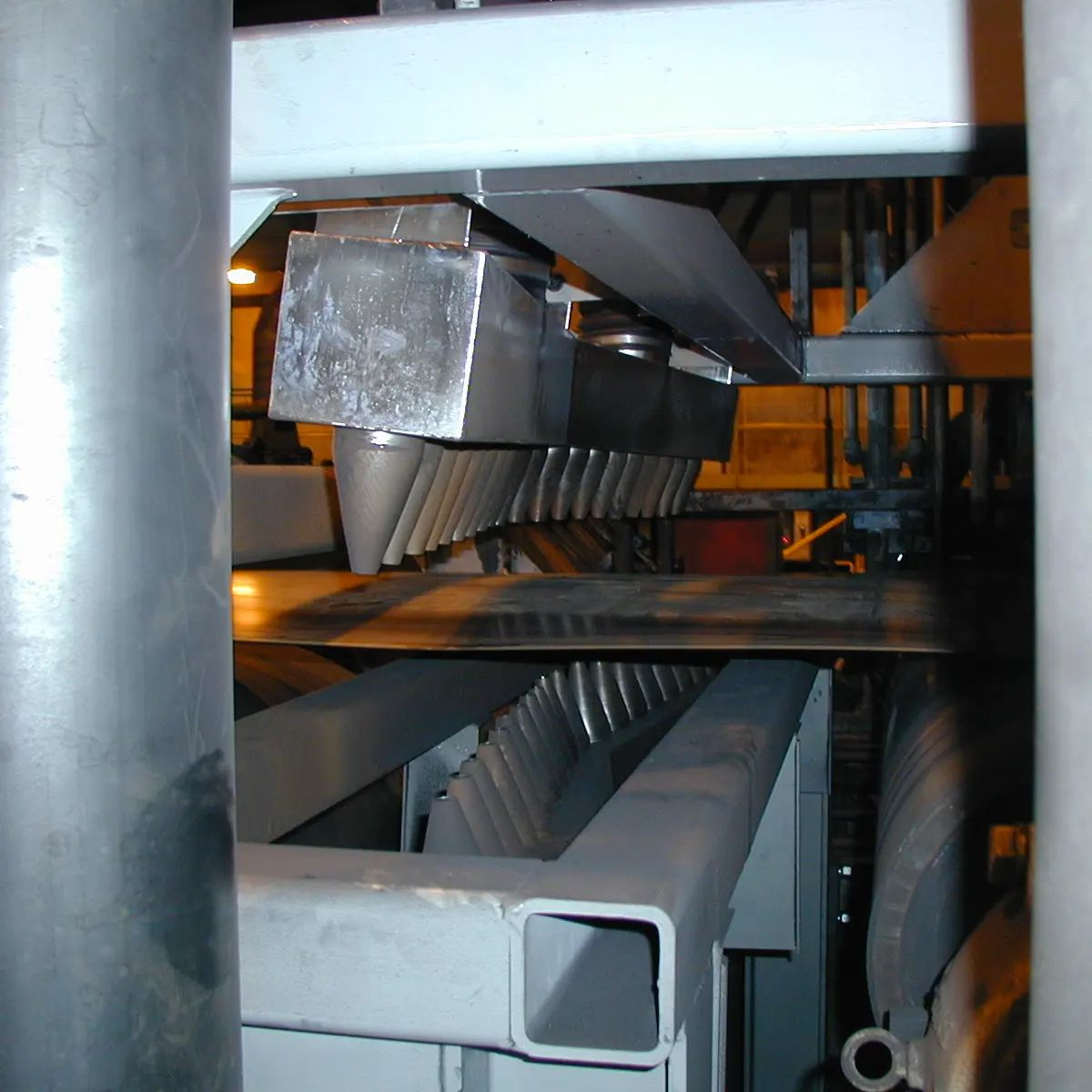
Frequently Asked Questions
Even when the buyer has selected the air knife and blower specifications based on past experience, it is still recommended that the supplier reviews the application and agrees with the buyer’s selections. Getting the air knife system supplier’s written quotation with the system performance guarantee assures the buyer gets properly sized equipment for the intended objective.
There are many factors in determining an effective and efficient air knife system, which include but are not limited to:
- Is the air knife system designed for a location >1000Ft ASL?
- List the min to max ambient air temp to the blower and min to max discharge air knife temp.
- Which accessory items have been quoted, and are there others that the customer may require?
- Are the materials of construction for the air knife system compatible with the application?
- Is the air knife zone an open area, or is it enclosed for control and containment of the blow-off process?
- What are the installation electrical supply details and motor control specs?
- Will the customer need to supply cooling water for a hot air or cold air knife system?
A general rule is that most air knives should be set with an angle of impingement at 10° to 15° from perpendicular and against (counter-current) to the product flow. The distance from the air knife outlets (slots or nozzles) to the product is a key factor in determining the system’s total blower horsepower. Although closer is better, which keeps the blower horsepower as low as possible, there are many successful air knife and air nozzle systems designed for maximum impact air velocity up to several feet from the knives or nozzles.
There are some air knife and air nozzle suppliers that categorize their performance by impact force in various units of pressure. It is far more relevant for blow-off force values to be expressed in units of impact air velocity as this relates directly to the shear force created to disrupt and displace a physical substance or thermal boundary layer from a product’s surface. Determining an appropriate impact air velocity for any given air knife application requires selecting a combination of exit air volume and air pressure at the air knife necessary to create the required shear force against the product. In reality, there can be dozens of application variables across a variety of industries, so it is best to work with air knife system designers who will guarantee their results while selecting the most effective and efficient air knife, nozzle, and blower system.
Adding hot air to air knives is a common request, but knowing what air temperature is truly required for the air knife application is the first question. Only a small percentage of applications need heat to supplement high-velocity air knives.
For the vast majority of continuous sheet and web coating drying applications, where 150°F-275°F IR or UV heater panels have been the standard for flash drying of water-based coatings, Sonic Air Systems’ patented “heater-less” hot air blower air knife technology is a proven game changer. In virtually every coating drying application, Sonic’s drying zone is less than 12” long; the air knife temps are 50-75% lower than heater panels, the total blower drying energy is 50% less, and most installations are simpler and lower cost.
The use of in-line electric closed coil tube heaters powered air knife systems plus large 3-phase heater control panels are commonly used, particularly when hot air knife systems must melt or keep in semi-molten state polymers and metalized coatings requiring 275F-1000°F temps. Sonic hot air knife technology cannot generate tube heater temperatures, but there are many other applications where the >275F temps are simply not necessary. Our hot air knives routinely produce equal or better drying results at much lower temperatures than many customers request, requiring up to 50% less energy with lower equipment and installation costs, while being an intrinsically safer system.
There are an increasing number of air knife applications across many industries where cold air from air knives at 10F to 50F is being used to cool products. Many city water systems are incentivizing their industrial users to reduce consumption and grey water discharge, so replacing water quench cooling of conveyed products with cold air offers many benefits. Sonic’s COOL-AIR in-line after-cooler system uses closed circuit cooling water (water tower of water/glycol) to reduce air knife air temperatures to approximately 10F above the temp of the closed circuit cooling water supply in order to maintain constant air knife temperatures with maximum air cooling efficiency. Cold air quenching prevents thermal stress on parts, uses less power than water blow-off air knife systems after water quench, and doesn’t require all of the support equipment for spraying water, containing water, or the filtration systems required before discharging the grey water to municipal systems.
It must first be noted that high-velocity air knives do not produce a static charge in parts onto which air is blowing. It is also true that wet surfaces of parts, after washing or spraying, do not hold a static charge and that water blow-off with air knives does not generate one.
Releasing static electricity from most clean surfaces or parts travelling on a conveyor requires only ionizing/static neutralizing bars without air knives. Whenever there are any statically charged surface particles or larger debris on webs or parts, a high-velocity air knife, together with an electrically powered ionizing bar, provides both effective blow-off and static neutralization of the particles and the surface/parts themselves.
The cleanliness of air blowing directly onto food products, food preparation surfaces, medical devices, and a wide variety of critical components going into high technology systems all demand the highest levels of air filtration available.
Every blower-powered air knife or air nozzle system receives its air from a rotating machine using standard air filters rated for 2-10 microns. Even if a HEPA air filter rated for 0.3 microns (a.k.a. MERV 17) is connected to the blower inlet, it is impossible to guarantee that the air from the blower will always meet critical cleanliness standards. The only way to guarantee intrinsically clean air, 0.3-micron air blowing onto critical products at all times, is by using a HEPA filter installed in-line after the blower.
When choosing an in-line HEPA filter, confirm the mounting arrangement, inlet & outlet connections, and flow rating are sized to match the blower it is to be used with.
High-velocity air knives blowing any liquid off products as they pass by on a conveyor, particularly when the air knife zone is enclosed within a tunnel, requires equipment to prevent the aerosol from affecting the surrounding factory environment while capturing and/or reusing the blow-off liquid as well as preventing the liquid or spray from the air knife action from re-contaminating the product surfaces which are being blown off. Optimizing the air knife positioning together with the tunnel design allows for bulk water to be effectively contained and directed to the drain lines for discharge.
Controlling the lighter aerosol component of blow-off spray requires a proper air exhaust design to enhance blow-off effectiveness by optimizing the exhaust air volume and velocity.
An experienced air knife system designer can provide guidance to help ensure the tunnel features and air balance to ensure success.
As a general rule, the optimal balance between air knife system efficiency and the cost of the piping and flex hose to deliver the blower air to the air knives is a design that has a minimum of 5% to a maximum of 10% air pressure loss through the piping and hose. Less than 5% losses mean that the piping/hose is larger in diameter and more expensive than needed. Greater than 10% pressure drop either causes less blow-off effectiveness or requires a larger horsepower and higher cost blower to make up for the small diameter piping or hose.
Although it is common to see piping or hose from the blower to air knives in the same diameter as the outlet size of the blower, there are many installations where the blower CFM and discharge air velocity are too high to allow for more than a few feet of piping or hose at the same diameter as the blower before the air friction losses exceed the 10% threshold.
In order to avoid costly plumbing redesigns, it is always best to have your air knife system provider assist with the piping and/or hose layout to optimize the sizing and cost of the air delivery system as well.
It is known in many industries that blower-power air knives typically operate at one or more orders of magnitude lower in decibel noise levels versus high-pressure compressed air knives and nozzles. Additionally, the audible hearing range of compressed air blowing out from knives and nozzles is at a much lower kHz frequency range as compared to most blower air knives. The higher kHz signatures of the blower air knife frequency mean that it is much easier to suppress airborne decibels to an acceptable level.
The effectiveness of basic panels or shields to block most of the line-of-sight air knife sound, together with the strategic use of readily available closed cell acoustical sound absorbing form, can generally achieve 10-15 dbA sound attenuation and even greater reductions with an air knife enclosure design optimized for each specific installation. There are certain high-velocity air impact applications where parts having air whistling through holes and over sharp part edges may need more help with those conditions, but there are generally sound reduction designs for most air knife installations.
Even when the buyer has selected the air knife and blower specifications based on past experience, it is still recommended that the supplier reviews the application and agrees with the buyer’s selections. Getting the air knife system supplier’s written quotation with the system performance guarantee assures the buyer gets properly sized equipment for the intended objective.
There are many factors in determining an effective and efficient air knife system, which include but are not limited to:
- Is the air knife system designed for a location >1000Ft ASL?
- List the min to max ambient air temp to the blower and min to max discharge air knife temp.
- Which accessory items have been quoted, and are there others that the customer may require?
- Are the materials of construction for the air knife system compatible with the application?
- Is the air knife zone an open area, or is it enclosed for control and containment of the blow-off process?
- What are the installation electrical supply details and motor control specs?
- Will the customer need to supply cooling water for a hot air or cold air knife system?
A general rule is that most air knives should be set with an angle of impingement at 10° to 15° from perpendicular and against (counter-current) to the product flow. The distance from the air knife outlets (slots or nozzles) to the product is a key factor in determining the system’s total blower horsepower. Although closer is better, which keeps the blower horsepower as low as possible, there are many successful air knife and air nozzle systems designed for maximum impact air velocity up to several feet from the knives or nozzles.
There are some air knife and air nozzle suppliers that categorize their performance by impact force in various units of pressure. It is far more relevant for blow-off force values to be expressed in units of impact air velocity as this relates directly to the shear force created to disrupt and displace a physical substance or thermal boundary layer from a product’s surface. Determining an appropriate impact air velocity for any given air knife application requires selecting a combination of exit air volume and air pressure at the air knife necessary to create the required shear force against the product. In reality, there can be dozens of application variables across a variety of industries, so it is best to work with air knife system designers who will guarantee their results while selecting the most effective and efficient air knife, nozzle, and blower system.
Adding hot air to air knives is a common request, but knowing what air temperature is truly required for the air knife application is the first question. Only a small percentage of applications need heat to supplement high-velocity air knives.
For the vast majority of continuous sheet and web coating drying applications, where 150°F-275°F IR or UV heater panels have been the standard for flash drying of water-based coatings, Sonic Air Systems’ patented “heater-less” hot air blower air knife technology is a proven game changer. In virtually every coating drying application, Sonic’s drying zone is less than 12” long; the air knife temps are 50-75% lower than heater panels, the total blower drying energy is 50% less, and most installations are simpler and lower cost.
The use of in-line electric closed coil tube heaters powered air knife systems plus large 3-phase heater control panels are commonly used, particularly when hot air knife systems must melt or keep in semi-molten state polymers and metalized coatings requiring 275F-1000°F temps. Sonic hot air knife technology cannot generate tube heater temperatures, but there are many other applications where the >275F temps are simply not necessary. Our hot air knives routinely produce equal or better drying results at much lower temperatures than many customers request, requiring up to 50% less energy with lower equipment and installation costs, while being an intrinsically safer system.
There are an increasing number of air knife applications across many industries where cold air from air knives at 10F to 50F is being used to cool products. Many city water systems are incentivizing their industrial users to reduce consumption and grey water discharge, so replacing water quench cooling of conveyed products with cold air offers many benefits. Sonic’s COOL-AIR in-line after-cooler system uses closed circuit cooling water (water tower of water/glycol) to reduce air knife air temperatures to approximately 10F above the temp of the closed circuit cooling water supply in order to maintain constant air knife temperatures with maximum air cooling efficiency. Cold air quenching prevents thermal stress on parts, uses less power than water blow-off air knife systems after water quench, and doesn’t require all of the support equipment for spraying water, containing water, or the filtration systems required before discharging the grey water to municipal systems.
It must first be noted that high-velocity air knives do not produce a static charge in parts onto which air is blowing. It is also true that wet surfaces of parts, after washing or spraying, do not hold a static charge and that water blow-off with air knives does not generate one.
Releasing static electricity from most clean surfaces or parts travelling on a conveyor requires only ionizing/static neutralizing bars without air knives. Whenever there are any statically charged surface particles or larger debris on webs or parts, a high-velocity air knife, together with an electrically powered ionizing bar, provides both effective blow-off and static neutralization of the particles and the surface/parts themselves.
The cleanliness of air blowing directly onto food products, food preparation surfaces, medical devices, and a wide variety of critical components going into high technology systems all demand the highest levels of air filtration available.
Every blower-powered air knife or air nozzle system receives its air from a rotating machine using standard air filters rated for 2-10 microns. Even if a HEPA air filter rated for 0.3 microns (a.k.a. MERV 17) is connected to the blower inlet, it is impossible to guarantee that the air from the blower will always meet critical cleanliness standards. The only way to guarantee intrinsically clean air, 0.3-micron air blowing onto critical products at all times, is by using a HEPA filter installed in-line after the blower.
When choosing an in-line HEPA filter, confirm the mounting arrangement, inlet & outlet connections, and flow rating are sized to match the blower it is to be used with.
High-velocity air knives blowing any liquid off products as they pass by on a conveyor, particularly when the air knife zone is enclosed within a tunnel, requires equipment to prevent the aerosol from affecting the surrounding factory environment while capturing and/or reusing the blow-off liquid as well as preventing the liquid or spray from the air knife action from re-contaminating the product surfaces which are being blown off. Optimizing the air knife positioning together with the tunnel design allows for bulk water to be effectively contained and directed to the drain lines for discharge.
Controlling the lighter aerosol component of blow-off spray requires a proper air exhaust design to enhance blow-off effectiveness by optimizing the exhaust air volume and velocity.
An experienced air knife system designer can provide guidance to help ensure the tunnel features and air balance to ensure success.
As a general rule, the optimal balance between air knife system efficiency and the cost of the piping and flex hose to deliver the blower air to the air knives is a design that has a minimum of 5% to a maximum of 10% air pressure loss through the piping and hose. Less than 5% losses mean that the piping/hose is larger in diameter and more expensive than needed. Greater than 10% pressure drop either causes less blow-off effectiveness or requires a larger horsepower and higher cost blower to make up for the small diameter piping or hose.
Although it is common to see piping or hose from the blower to air knives in the same diameter as the outlet size of the blower, there are many installations where the blower CFM and discharge air velocity are too high to allow for more than a few feet of piping or hose at the same diameter as the blower before the air friction losses exceed the 10% threshold.
In order to avoid costly plumbing redesigns, it is always best to have your air knife system provider assist with the piping and/or hose layout to optimize the sizing and cost of the air delivery system as well.
It is known in many industries that blower-power air knives typically operate at one or more orders of magnitude lower in decibel noise levels versus high-pressure compressed air knives and nozzles. Additionally, the audible hearing range of compressed air blowing out from knives and nozzles is at a much lower kHz frequency range as compared to most blower air knives. The higher kHz signatures of the blower air knife frequency mean that it is much easier to suppress airborne decibels to an acceptable level.
The effectiveness of basic panels or shields to block most of the line-of-sight air knife sound, together with the strategic use of readily available closed cell acoustical sound absorbing form, can generally achieve 10-15 dbA sound attenuation and even greater reductions with an air knife enclosure design optimized for each specific installation. There are certain high-velocity air impact applications where parts having air whistling through holes and over sharp part edges may need more help with those conditions, but there are generally sound reduction designs for most air knife installations.