CASE STUDIES
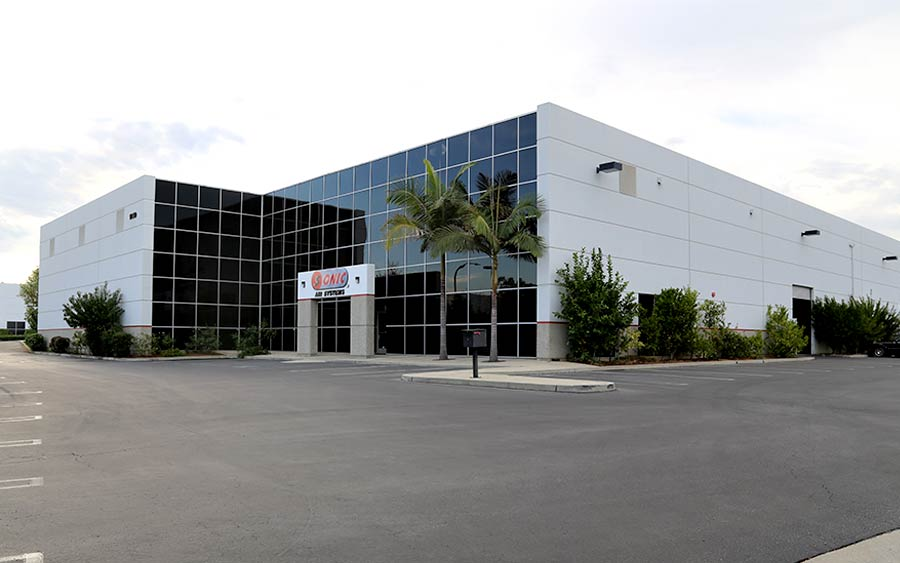
How Sonic Hot Air Knife System Drives IQF Process Water Conservation
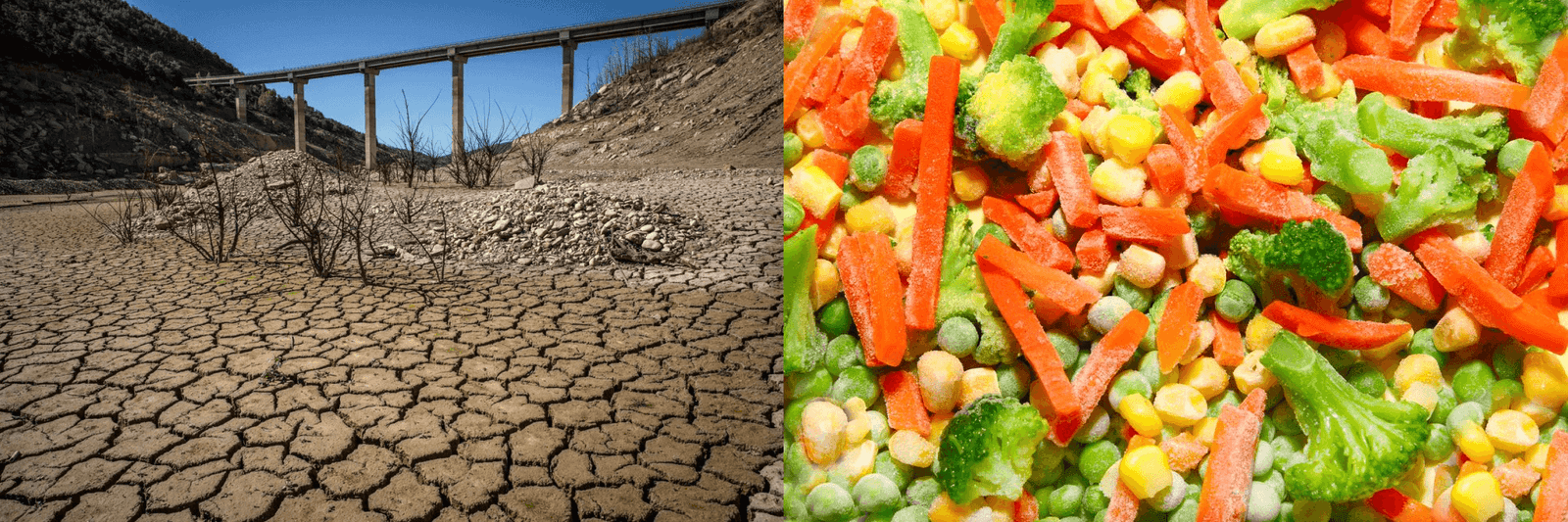
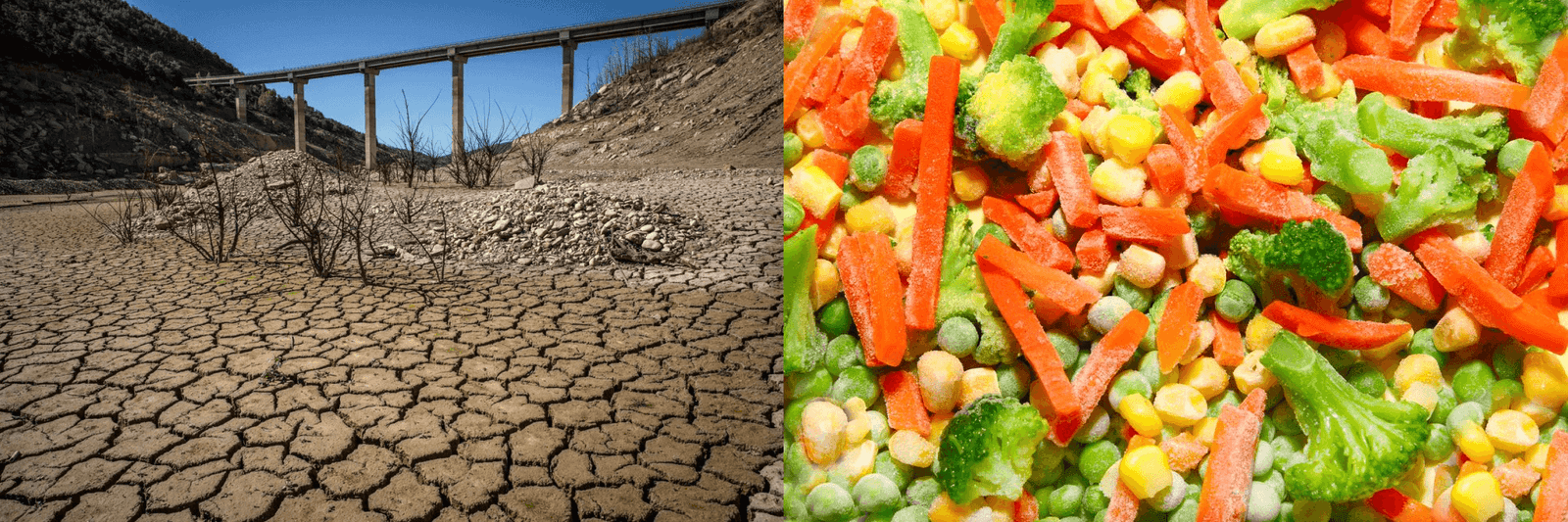
Overview
In 2022, California experienced its worst drought in over a century. This created a huge problem for the largest Individual Quick Freezing (IQF) processor of vegetables in the US, which is based in the fertile Central Valley of California and uses thousands of gallons of water daily in its production process.
The IQF process involves sending sliced and diced vegetables on a conveyor belt into a blast chiller that freezes them individually very quickly. After the IQF process, warm water is sprayed on the conveyor to de-ice the belt, as ice crystals form on the belt during the procedure. This production process repeats itself, going from clean to iced belt to de-icing the conveyor belt, using tons of precious water resources.
During the drought, the IQF processor faced the challenge of reducing its water consumption while maintaining its production levels and product quality.
Solution
The IQF processor reached out to Sonic Air Systems for an alternative water-saving solution that eliminates the water spray bar. Sonic offered a two-pronged solution:
- A Sonic high-velocity Air Knife System first removes any excess pieces of vegetables stuck in the perforations of the conveyor belt.
- A second Sonic patented hot air knife system produces 150˚ F (65.5˚ C) high-velocity heated air to warm and prevent ice damage to the conveyor belt. This eliminates the need for water in de-icing conveyor belts for both in-line and spiral freezer belt washers.
Result
The customer successfully achieved its objectives of IQF process water conservation and cost savings, reducing both water and power usage. Despite the recent atmospheric river storms that brought drought relief to California in 2023, long-term groundwater restoration is still a problem in many parts of the Western USA. Sonic Air Systems provides a proactive water-saving solution for the long term.
Related Products
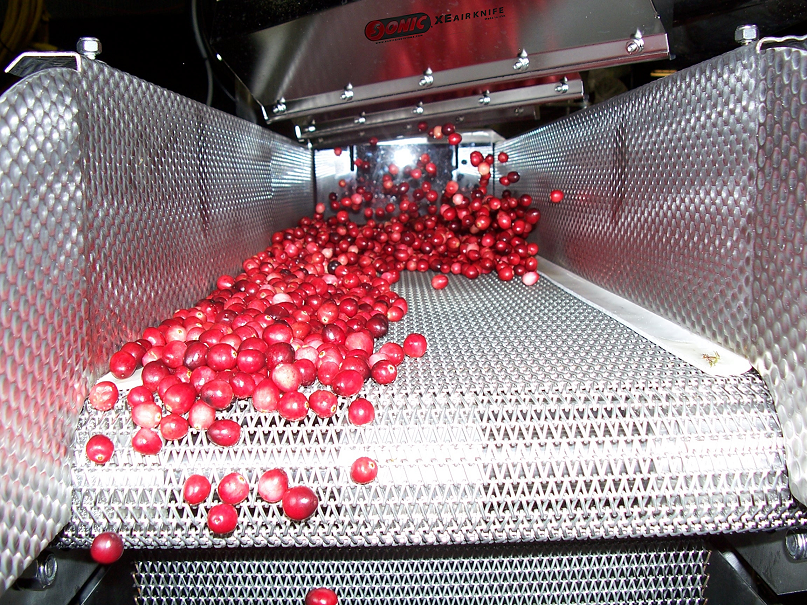
Food and Beverage
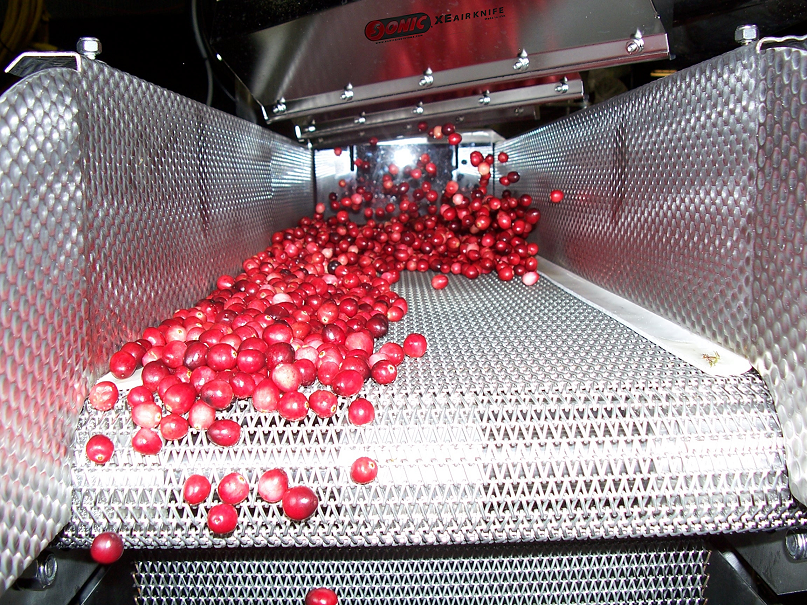
Food and Beverage

Hot Air Knife Systems (Patented)

Hot Air Knife Systems (Patented)
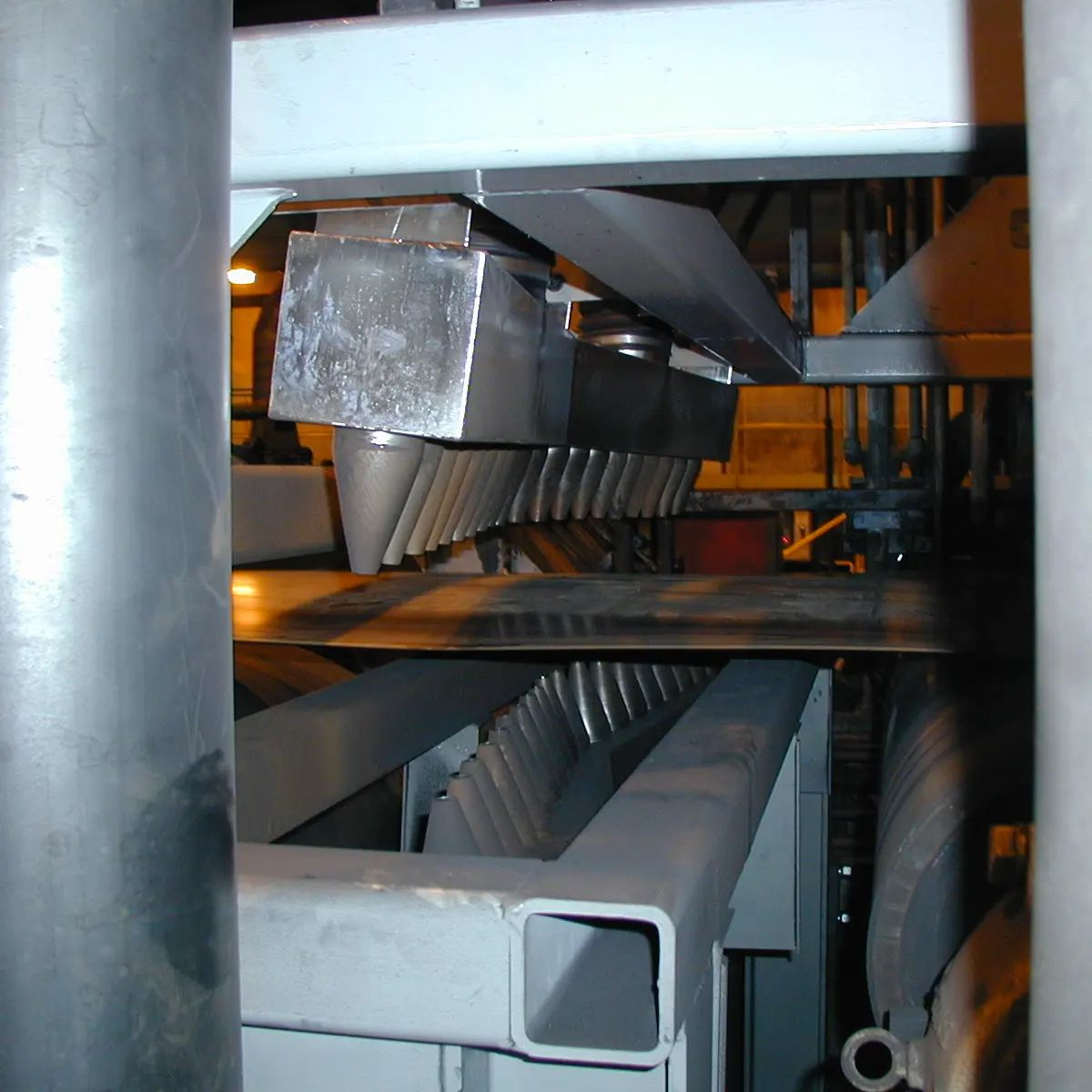