CASE STUDIES
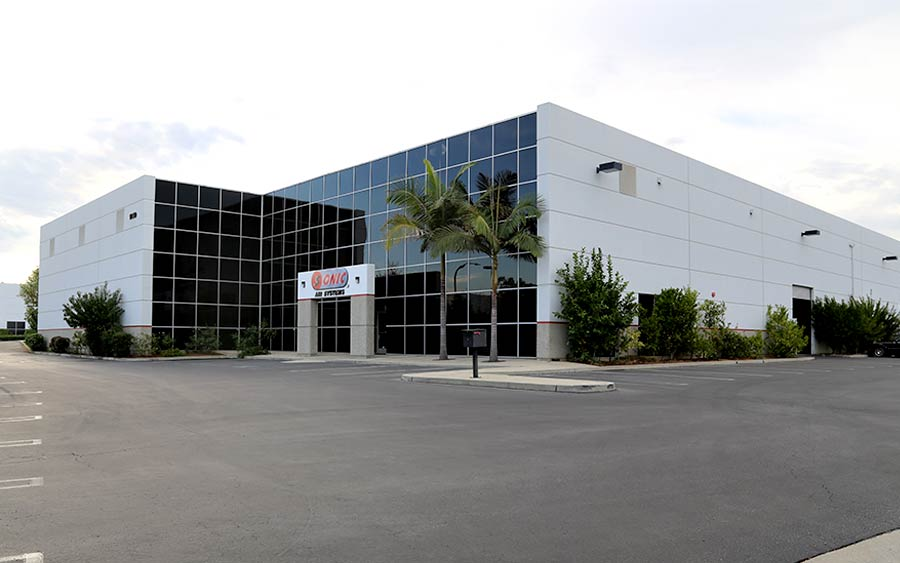
Sonic Eliminates Belt Scrapers & Doctor Blades with Non-Contact Air Knife Systems
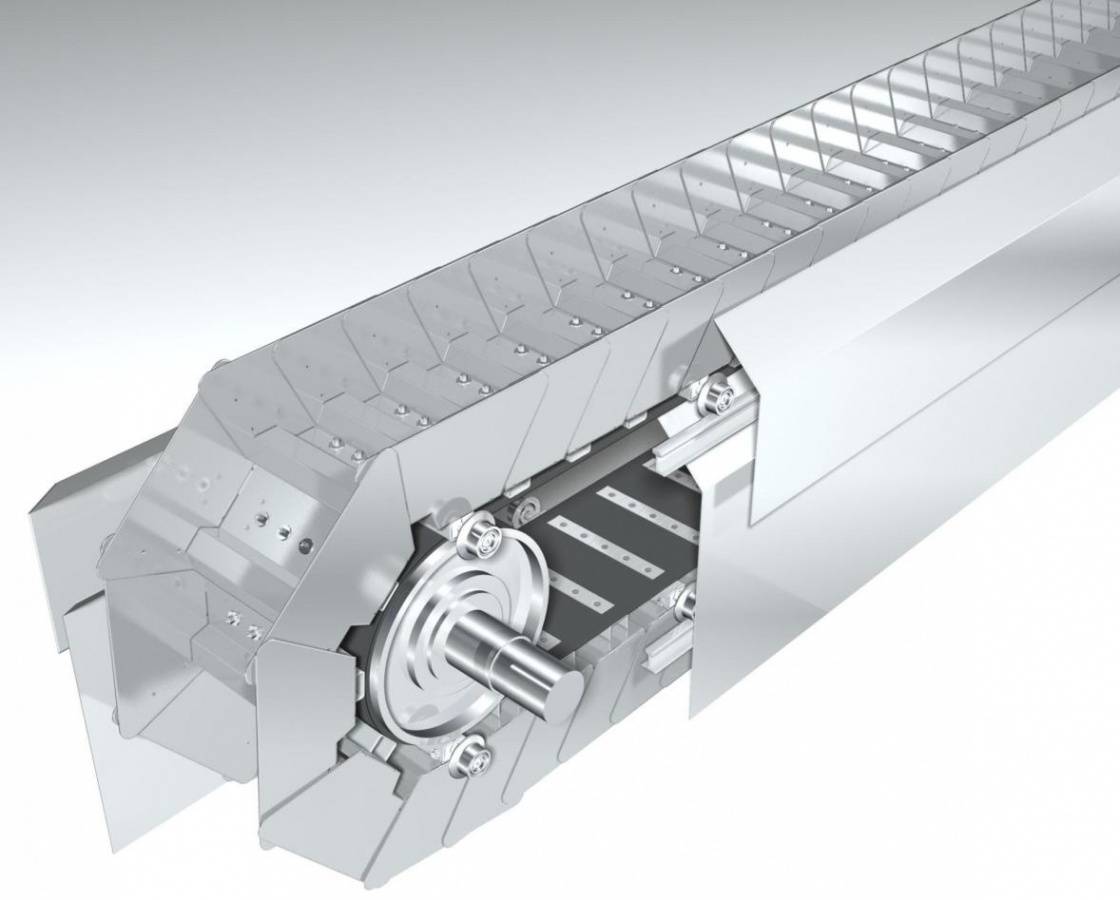
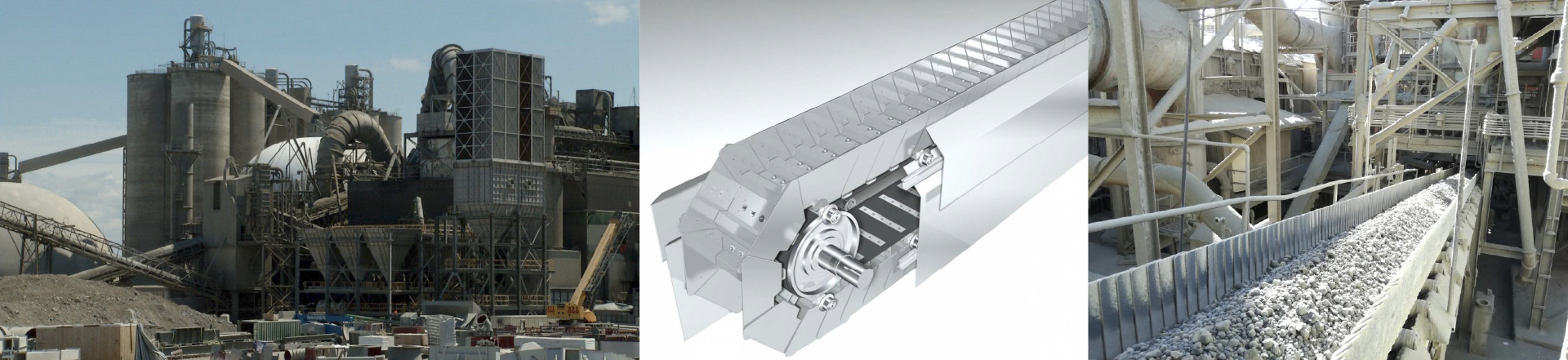
Overview
Around the world, various mining materials and other refined compounds are transported using flat belt conveyors to the next stage of processing. When these conveyors handle wet or sticky products, they must rely on the continuous wearing scraper blades, also known as doctor blades, to remove excess materials left on the belt after the head pulley.
However, many conveyed materials with little or no moisture content also utilizes contact scraper blades to remove the excess powdery product, but they do little to reduce the airborne dust produced by the blade. As belt scrapers wear down, they become less effective, leading to more frequent blade maintenance and replacement, potential belt damage, and increased volumes of airborne dust.
Due to stricter local and national limits on industrial particulate emissions, the cement industry is increasingly focused on improving pollution controls. By containing a higher percentage of fugitive cement clinker, they can pay for their newest pollution compliance, making today’s blower-powered, non-contact, high-velocity air knife systems a win-win solution.
Today, cement clinker capture is one of the most common conveyor belt blow-off applications for Sonic Air.
Solution
With most clinker belts ranging in width from 24" to 36" (61cm-92cm) and belt speeds up to 400 FPM (122 m/min), Sonic provides a 7.5-10Hp (5.5-7.5kW) blower powering a Sonic non-contact XE series high-efficiency air knife producing exit air velocities to 31,500 FPM (160 m/sec).
These compact Sonic air blowers are usually close-coupled to the Sonic air knife. These clinker blow-off systems are suitable for high dust load conditions because they are protected by a Sonic 2-stage air filter. This ensures that the number of air filter maintenance cycles and the total annual costs are a fraction of a typical pleated cartridge filter.
Result
The non-contact Sonic XE air knife system blows away all excess clinker products and residual powders from the belt while directing the air and powder into the customer’s central dust collector inlet. This is where airborne particulate is contained to meet air quality requirements while also reducing valuable product loss to near zero. Thanks to these improvements in safety, product yield, and operating efficiency, Sonic has become the standard for many of North America's largest cement companies.
Related Products
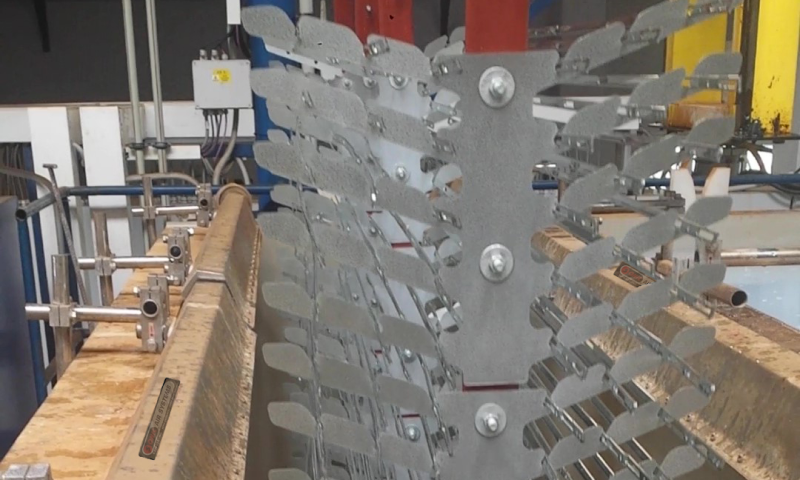
Industrial Air Knife Systems
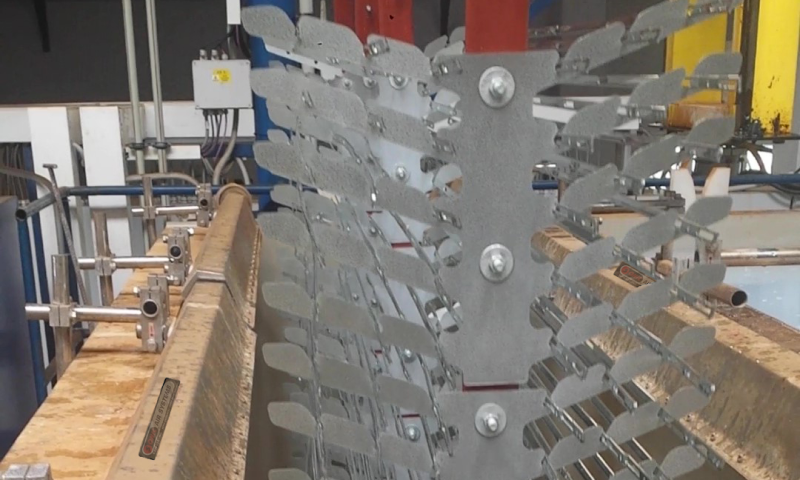
Industrial Air Knife Systems
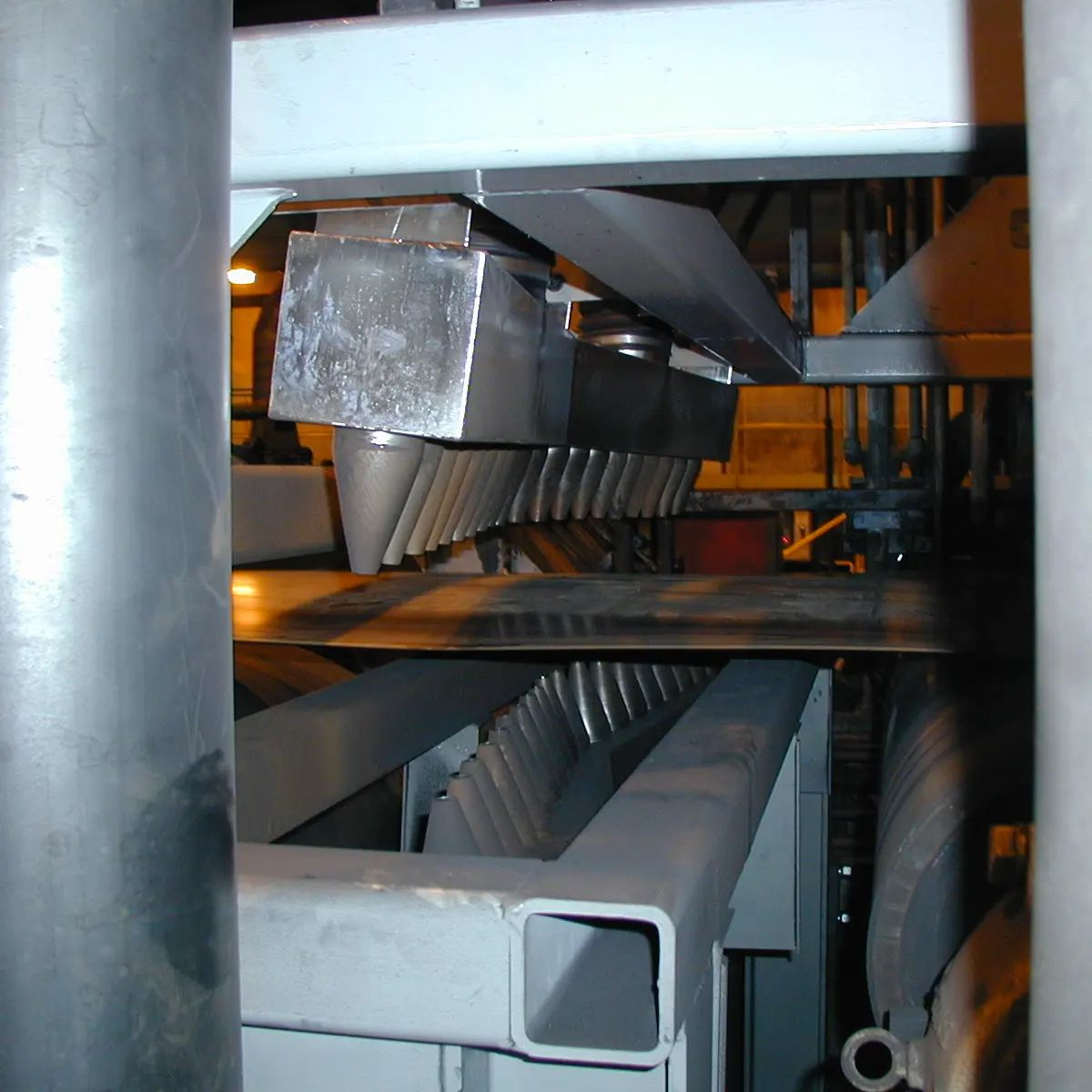