CASE STUDIES
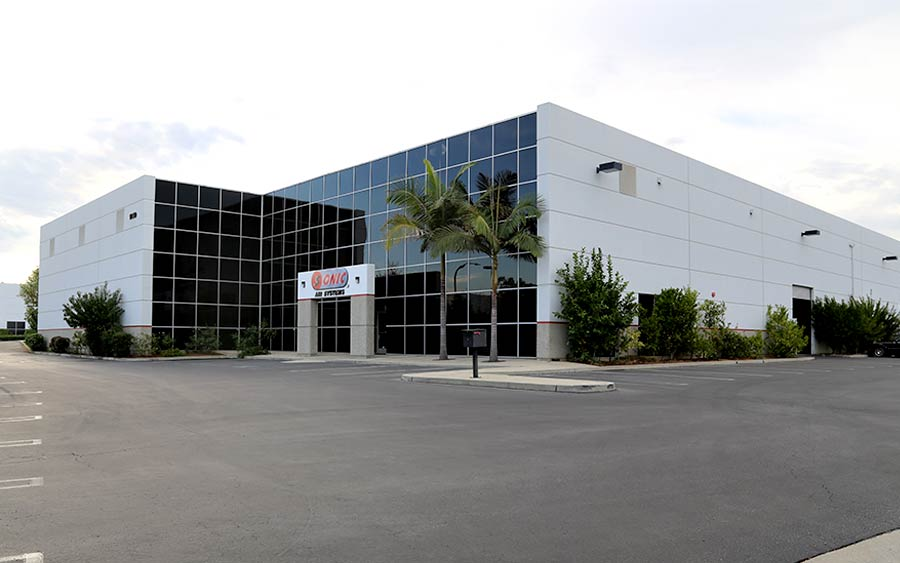
Driving Quality and Sustainability with Air Nozzle Systems for Nestle's Candy Packaging
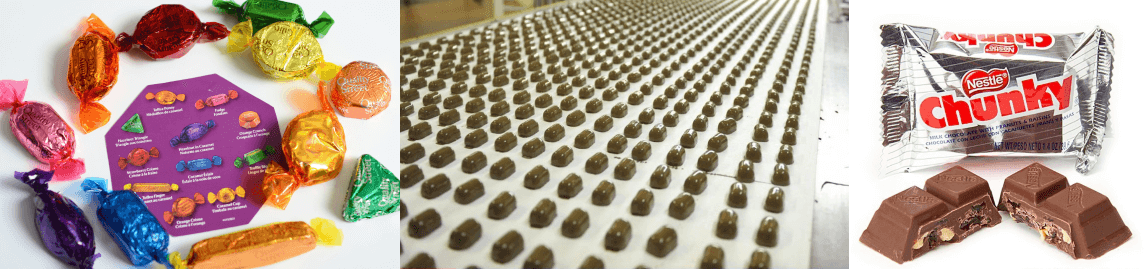
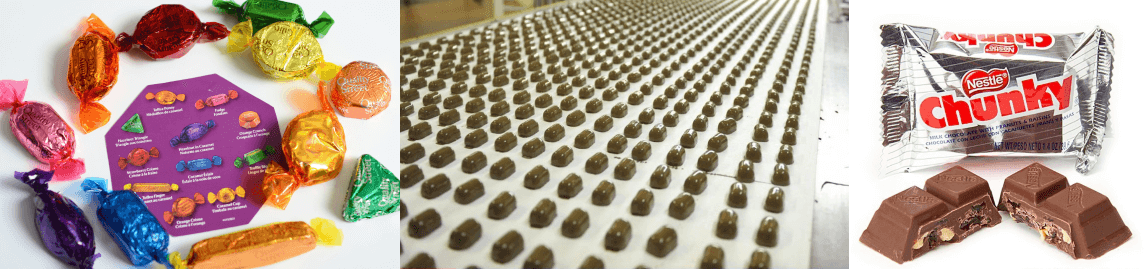
Overview
Nestle, a global food and beverage industry leader renowned for its iconic brands, sought to improve packaging quality, reduce waste, and achieve energy savings. Nestle approached Sonic Air Systems to address a specific challenge: replacing energy-intensive compressed air nozzles for the food industry while enhancing the handling of a small percentage of candies that were rejected from final packaging due to non-compliant wrapper registration. Nestle desired a solution that could separate the non-conforming wrappers from the product, enabling the candies to continue for re-processing.
Solution
Sonic collaborated with Nestle's conveyor vendor to develop a customized solution. The design included an enclosed conveyor system with specific dimensions and cleated dividers to hold a maximum of 10 rejected items per enclosed conveyor pocket. Sonic designed a high-speed blower and air nozzle system to create a high-velocity cyclonic movement of the rejected items, ensuring effective candy wrapper blow-off. An air eductor, powered by the same blower, provided a light vacuum to suck the wrappers up through a dedicated port, diverting them through a scrap product air ejector pipe while allowing the milk chocolate products to be re-processed. The Sonic Air Nozzle System, equipped with an in-line HEPA filter for hygienic compliance, delivered the required high-velocity amplified air to replace the energy-intensive compressed air nozzles.
Result
Sonic’s' Air Nozzle Systems enabled Nestle to achieve remarkable packaging quality control and sustainability outcomes. The results included energy savings by replacing a 75 HP (56 kW) compressed air nozzle system with Sonic's 15 HP (11kW) air blower, improved packaging quality through effective separation of non-conforming wrappers, reduced waste by re-processing candies, and support for Nestle's sustainability initiatives. The collaboration between Sonic and Nestle has revolutionized food and beverage packaging quality control, setting a new industry standard.
Related Products
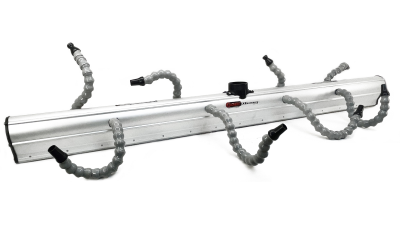
Air Nozzle & Air Nozzle Manifolds
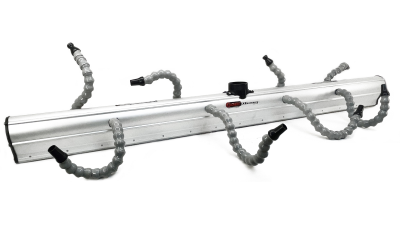
Air Nozzle & Air Nozzle Manifolds
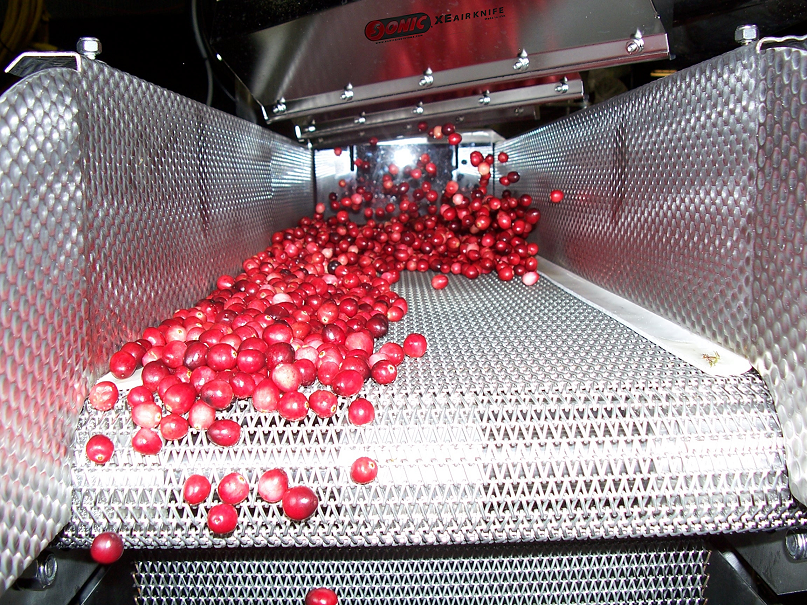
Food and Beverage
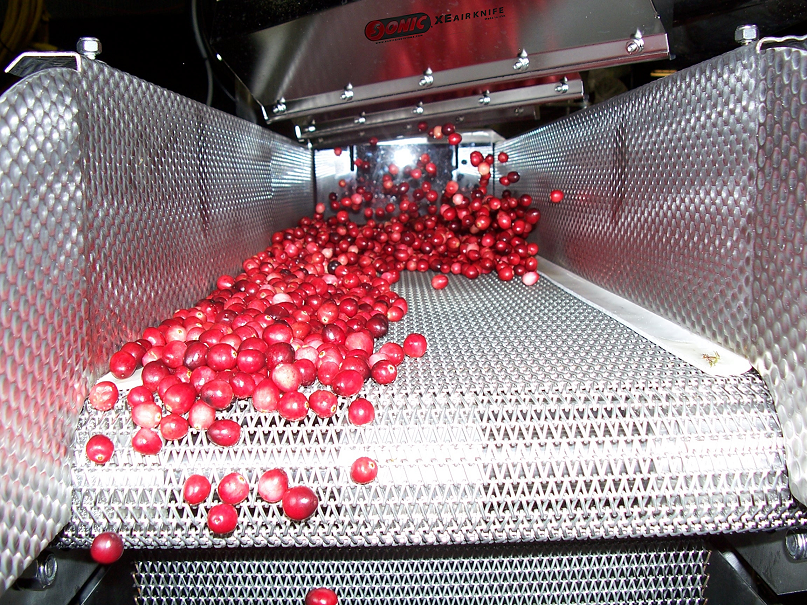
Food and Beverage
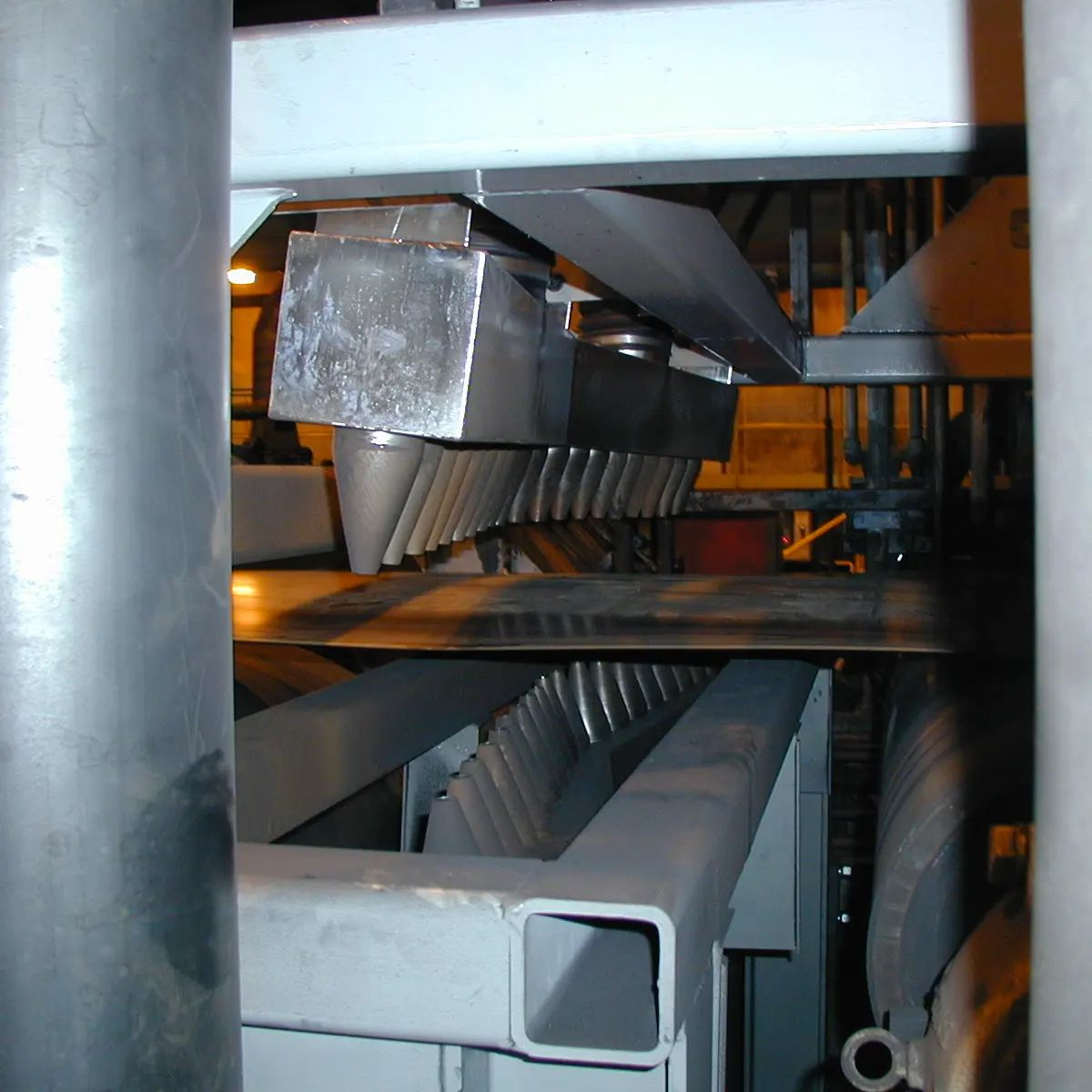