CASE STUDIES
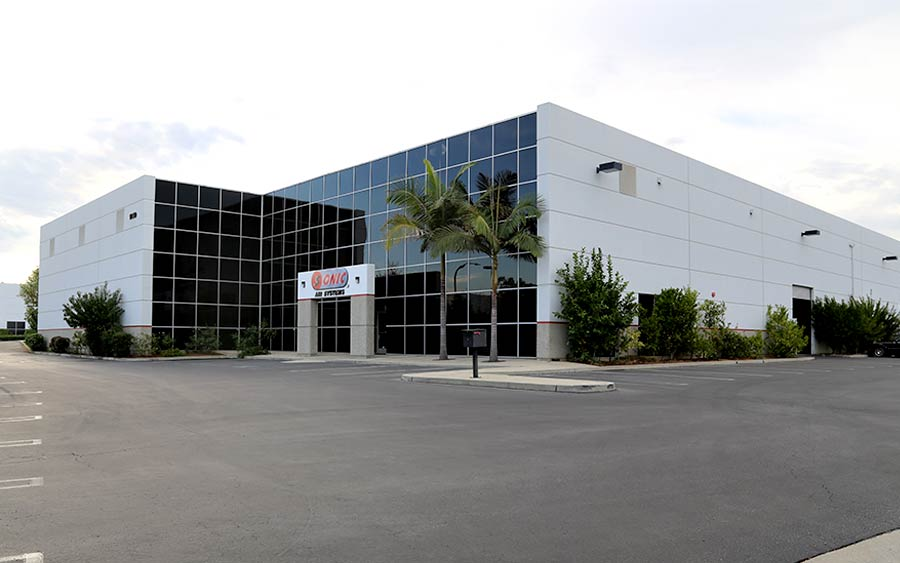
Sonic’s Industrial Air Knife Systems Help Japan Bus Manufacturer Finish In 1st Place For Quality At The Tokyo 2020 Olympics
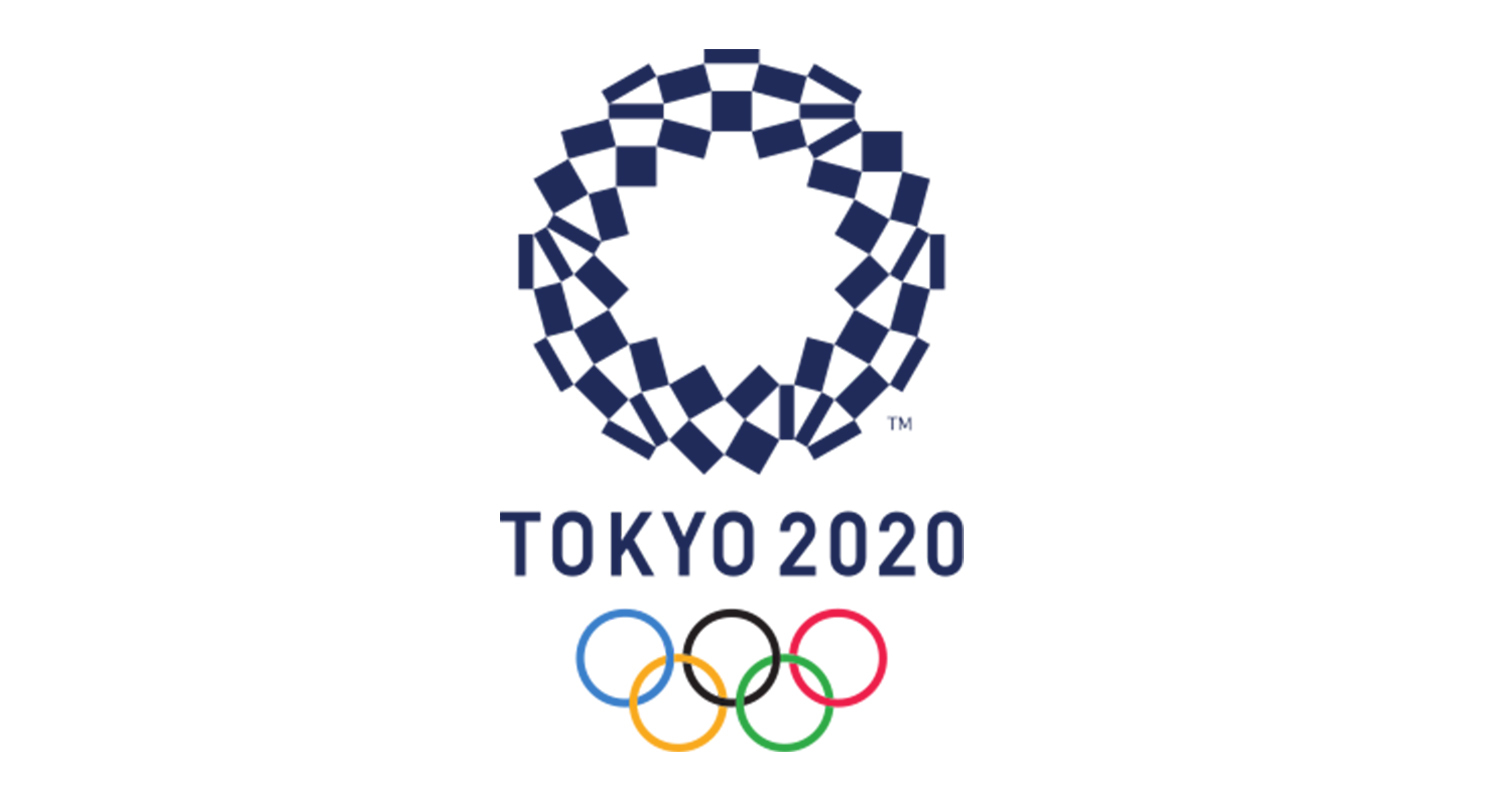
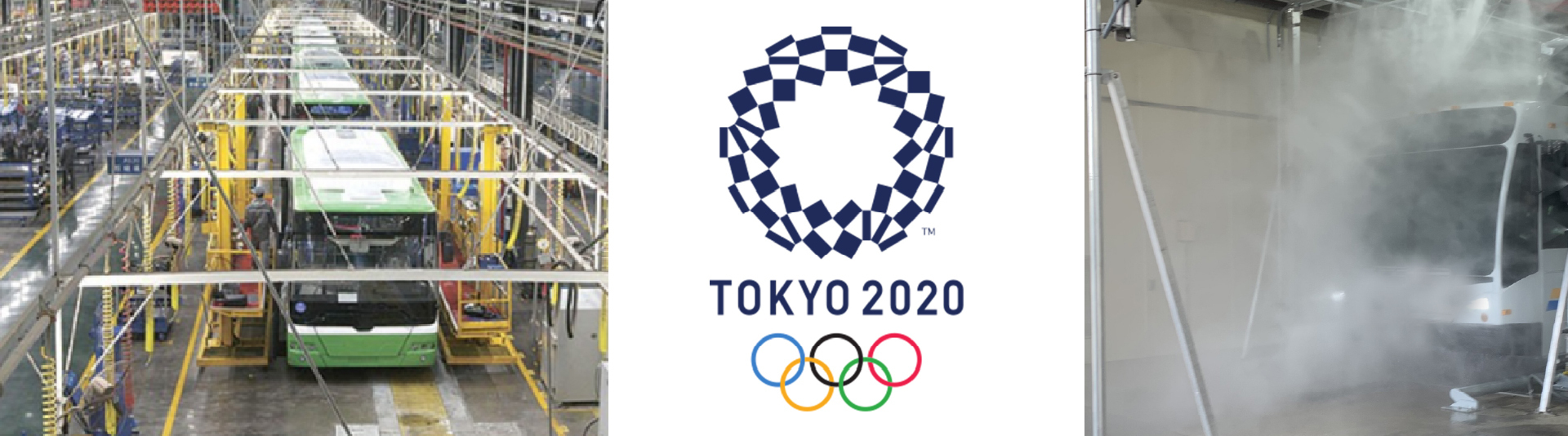
Overview
As Japan's premier manufacturer of buses and coaches prepared its new fleet of vehicles to carry athletes and spectators for the Tokyo 2020 Olympics, the Japanese government emphasized the safety and comfort of everyone amid the global COVID pandemic. This made the fit and finish of the latest generation of transport more crucial.
Solution
Their supplier, a provider of technical fluid transport supply systems, selected Sonic Air Systems to partner on this high-profile project. The four models of buses – Large-Size, Midsize, Shuttles, and Connecting Buses go through rigorous quality tests and inspections. Windows and doors are installed after the various coats of paint are applied to the outer bodies of the buses. High-pressure water sprays are targeted at the windows and doors as part of the leak testing process to ensure they are 100% waterproof. After the Quality Assurance in automotive inspects the interior of the bus for leaks, water spray needs to be removed from the exterior of the buses.
Sonic Blower powered 25HP (18.5kW) Industrial Air Knife Systems dries all four models of new buses, ranging in size from 9 mL X 2.3m W X 3m H (29.5ft L X 7.5ft W X 10ft H) to 18 mL X 2.9m W X 3.26m H (59ft L X 9.5ft W X 10.7ft H) after the leak testing. The Sonic Industrial Blower, which was housed in a stainless steel enclosure to protect it from water overspray, also met the stringent JISHA Regulations (the Japanese equivalent of OHSA) of less than 80dbA.
Result
Sonic was chosen as a partner in quality assurance in automotive due to recommendations from other Japanese manufacturers. With a strong presence in the automotive industry, Sonic plays a key role in processes such as water removal during metal forming and fabrication, debris blow-off during machining and painting/coating, and static neutralization of plastic and electronic components. We have helped clients overcome quality challenges, save on energy costs, reduce raw material waste, and eliminate the need for labor, recycling, and more, all while ensuring effective automotive shower testing systems are in place.
Related Products
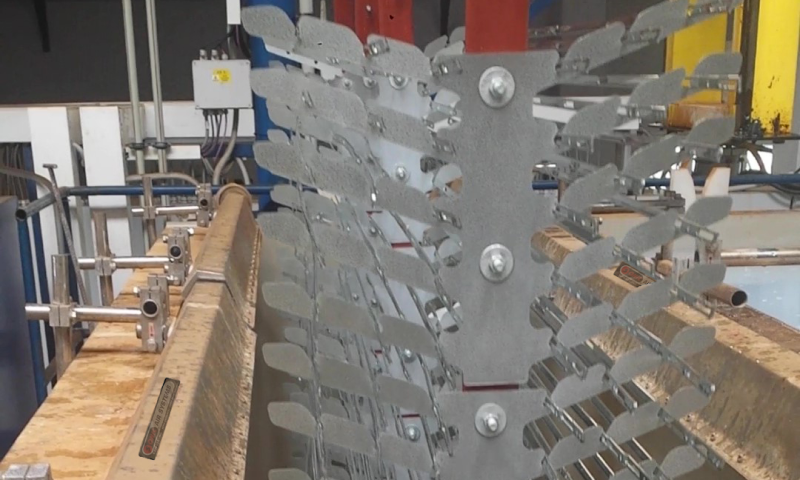
Industrial Air Knife Systems
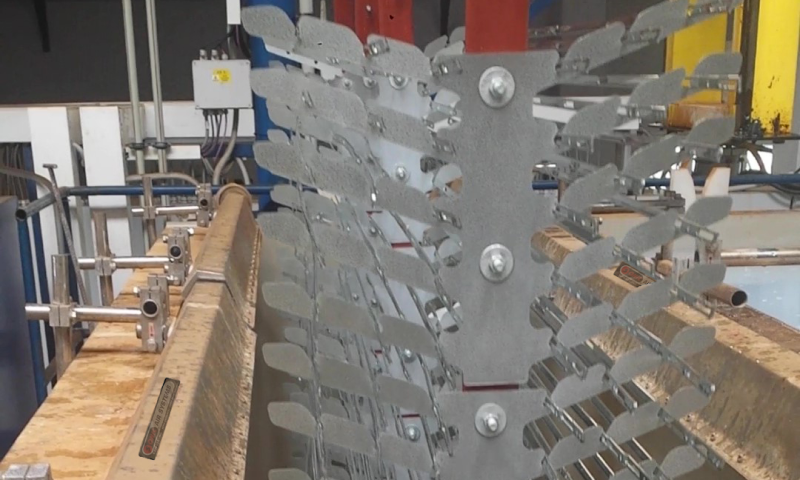
Industrial Air Knife Systems
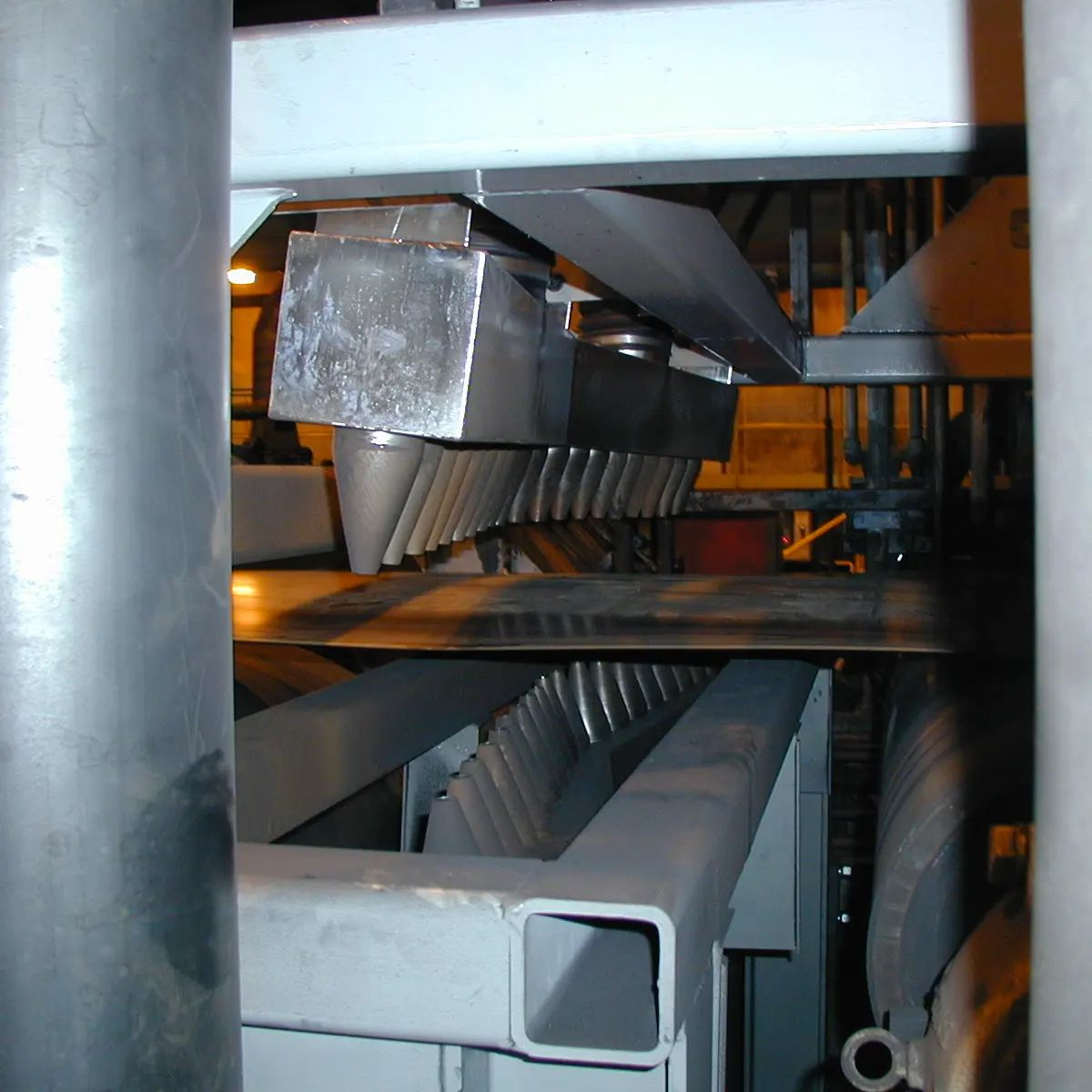