CASE STUDIES
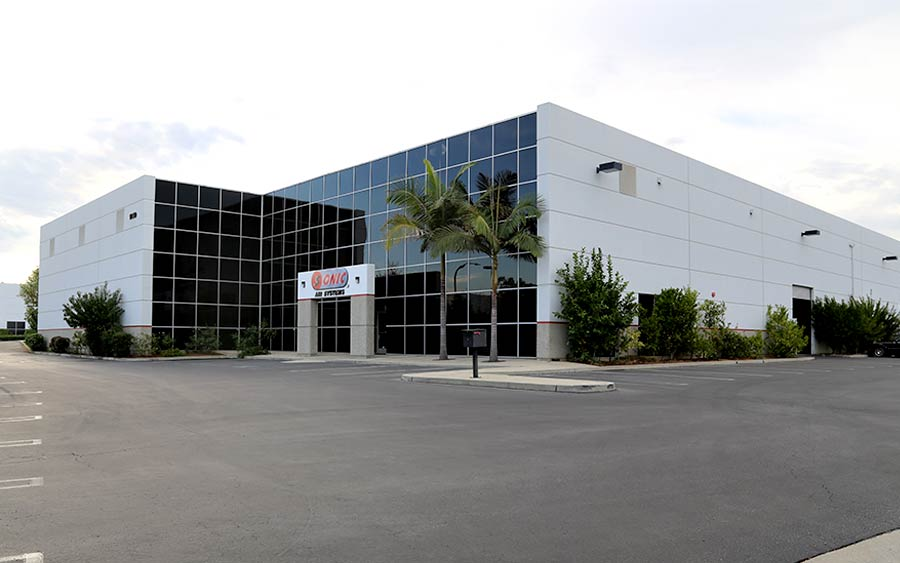
Redefining Standards with Dual Air Knife Systems for Temperature Control, Debris Blow-off, and Floor Safety
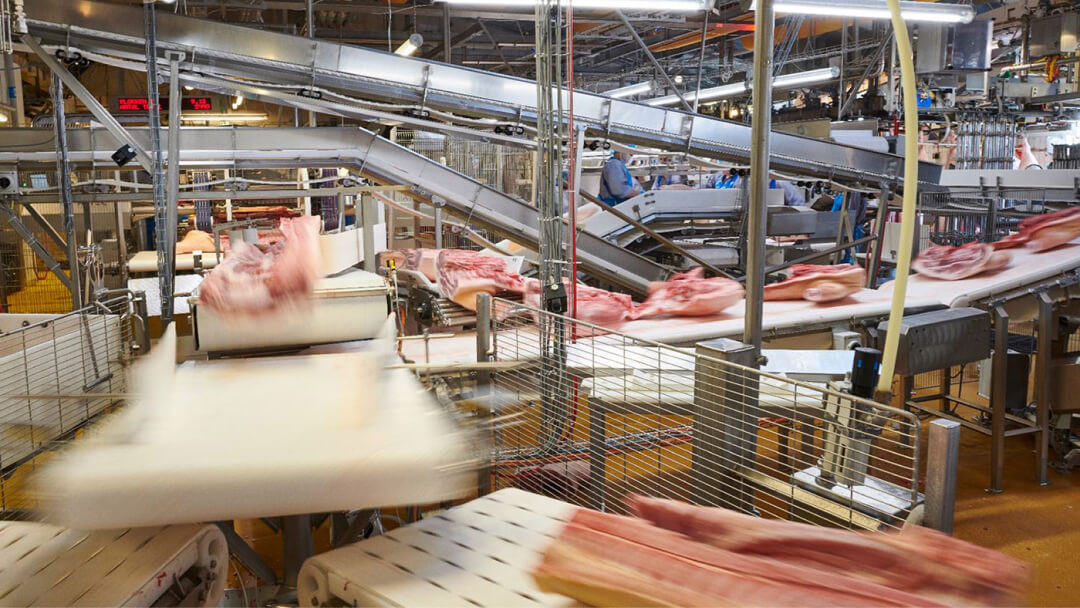
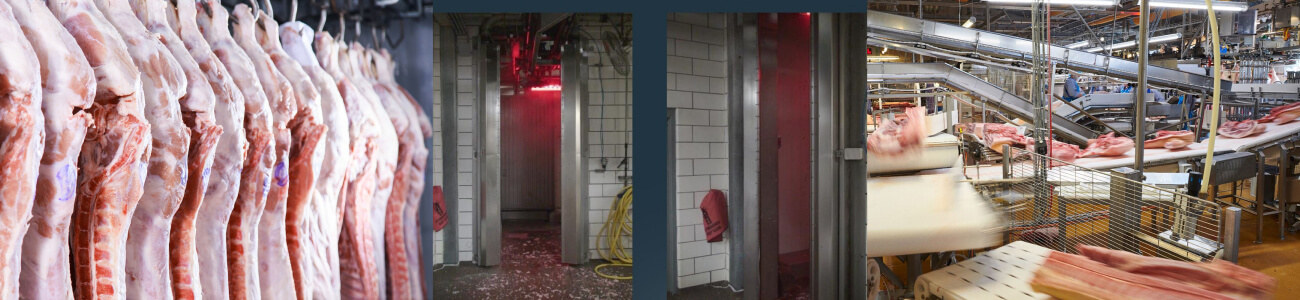
Overview
Industrial air curtains, commonly known as air doors, provide temperature control and act as an invisible barrier at entrances. However, when additional objectives such as debris or liquid blow-off are involved, traditional commercial door-mounted fans may fall short. A leading Pennsylvania meat plant faced multiple challenges, including temperature control, escalating energy costs, and frost formation on the floor of their freezer room. In collaboration with their local agent Technical Products & Services, Sonic Air Systems provided a customized solution using a dual air knife system to address these challenges in cold room curtains effectively.
Solution
Sonic designed and engineered a dual air knife system for the 10 ft (3 m) high doors of the meat plant's freezer room. The system served three key objectives: preserving cold air by preventing its escape, effectively blowing off excess antimicrobial spray from pig carcasses, and eliminating frost formation on the floor outside and inside the freezer. Sonic's energy-efficient Air Curtain Systems were tailored to suit the application's specific requirements, ensuring optimal performance, energy efficiency, and cost-effectiveness.
Result
The Sonic Air Knife System was purchased to reduce refrigeration load by creating an effective air seal at the freezer entrance. However, the 9-month ROI didn't anticipate the equally beneficial improvements to worker safety, including increased visibility in the freezer room due to reduced temperature gradient fog and frost formation in the freezer doorway, as well as a reduction in antimicrobial rinse water dripping on the floor, all due to the high air velocity blow-off created by the Sonic air knife systems.
Related Products
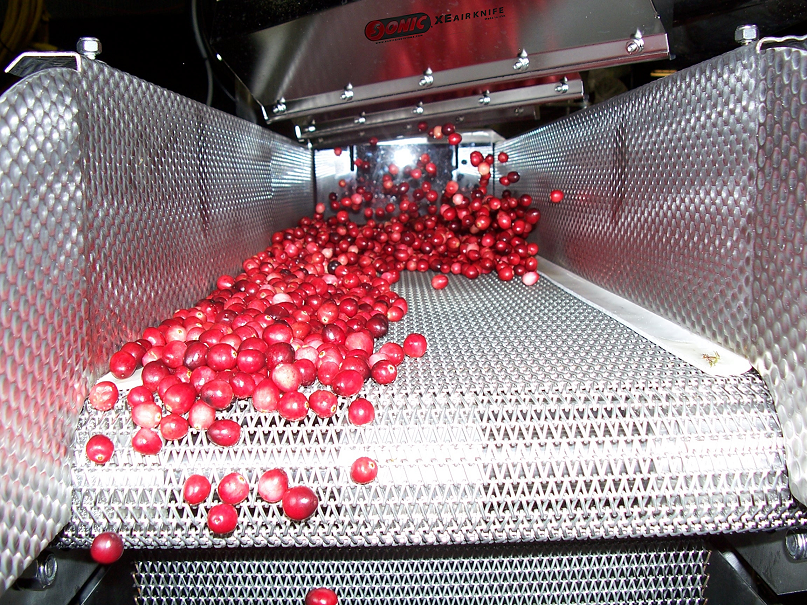
Food and Beverage Air Knife Systems
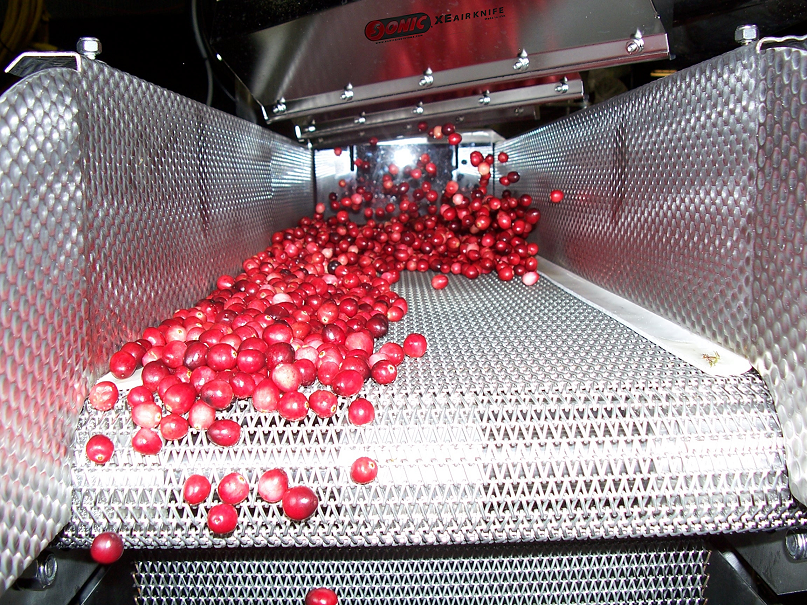
Food and Beverage Air Knife Systems
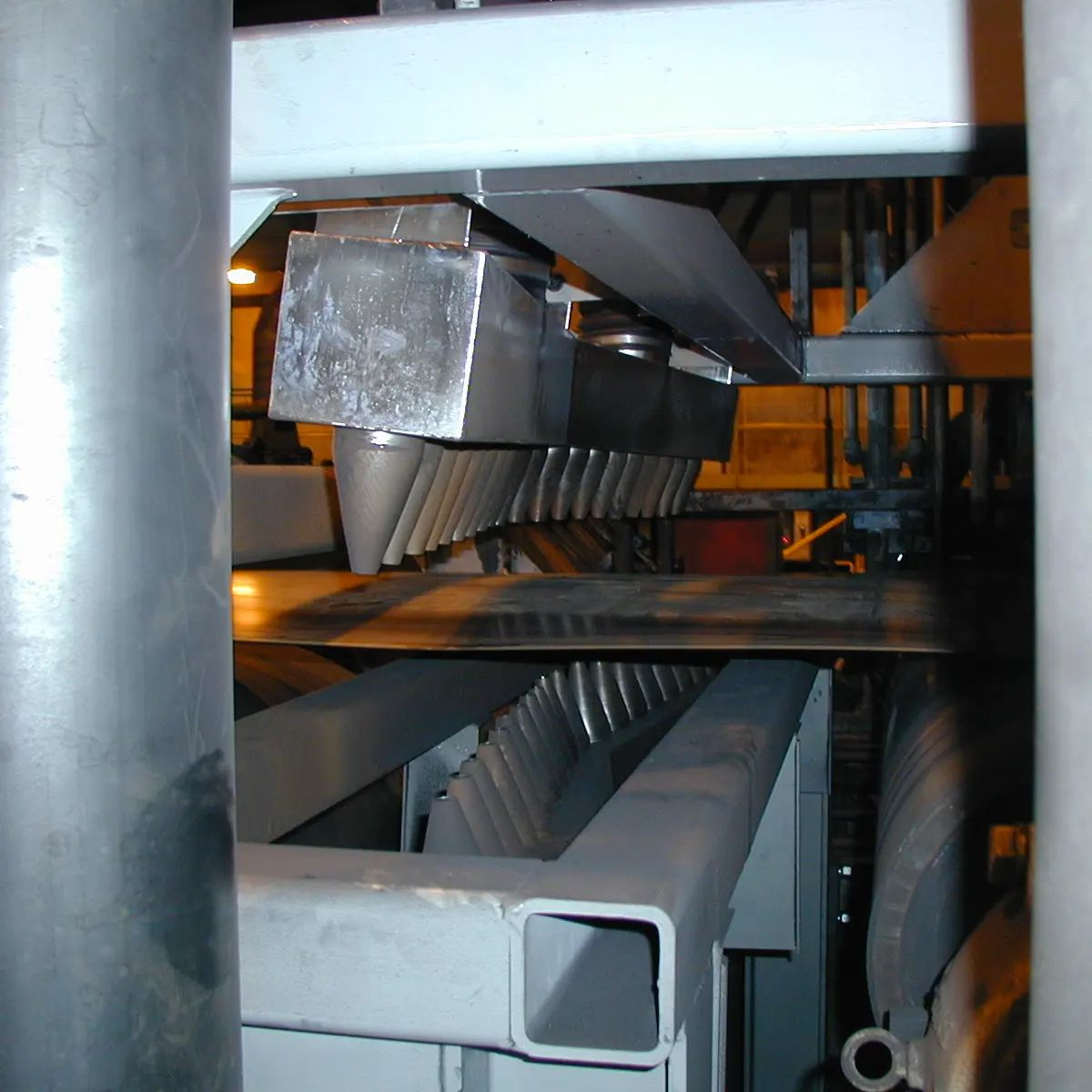