CASE STUDIES
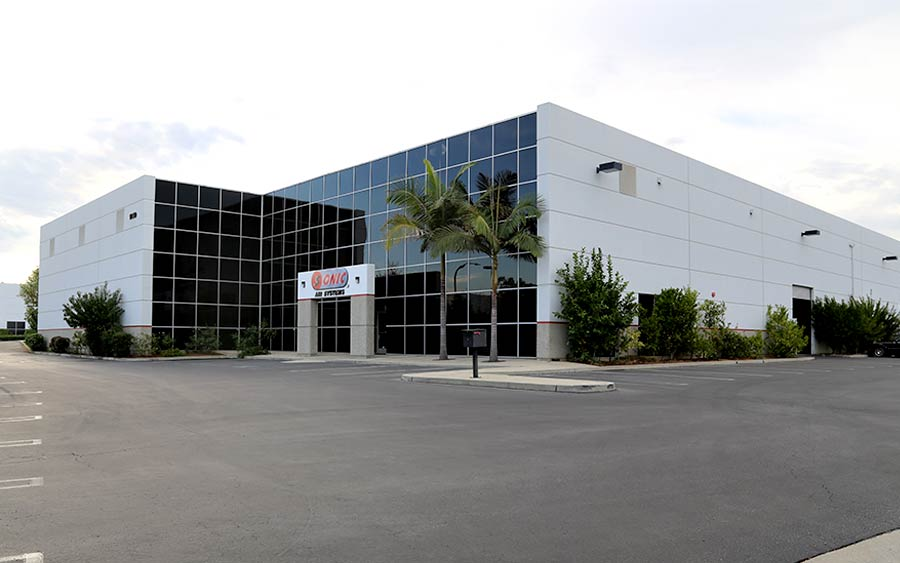
15 Years of Energy-Efficiency and Peak Performance with Sonic's Sanitary Air Knife System
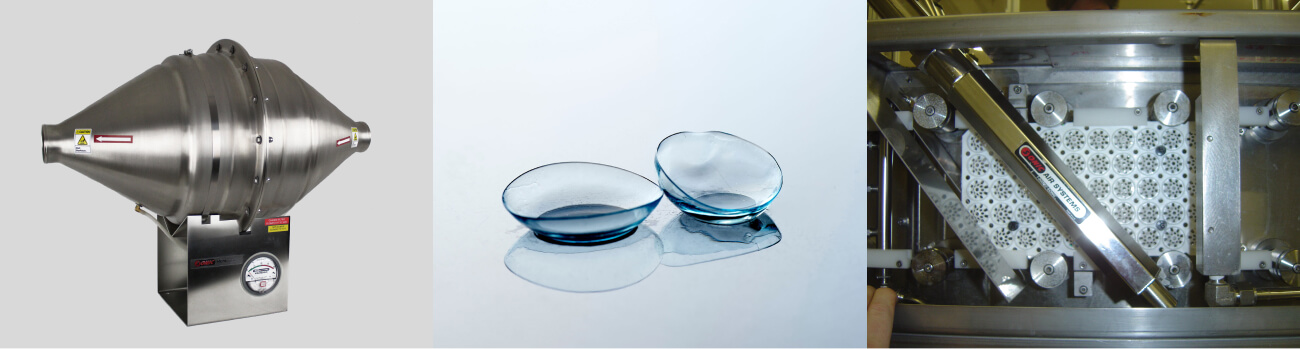
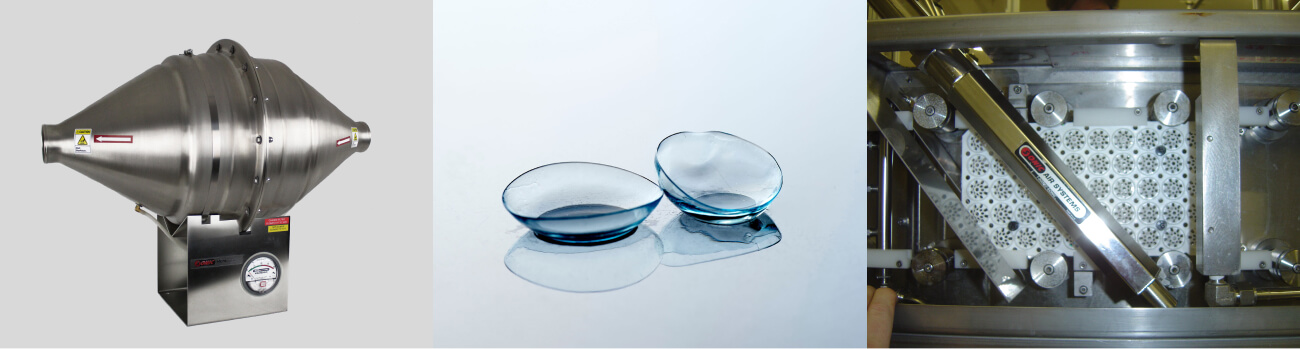
Overview
A leading contact lens manufacturer faced the challenge of drying hundreds of pairs of contact lens pallets in a sanitary and efficient manner. Significant energy consumption and frequent drying system maintenance prompted the need to replace the existing compressed air knife system.
Solution
Sonic Air Systems, a leader in medical device drying applications, was asked to offer a custom sanitary air knife tailored to fit the manufacturer's existing enclosure. Sonic's 95% efficient XE Air Knives were combined with in-line HEPA filters to ensure clean and dry air for pallet drying. Sonic supplied a single 7.5 HP (5.5kW) blower and HEPA filter for each pair of Sonic Sanitary Air Knife across all production lines.
Result
By implementing hygienic air knife systems, the contact lens manufacturer achieved a net energy savings of 64% compared to the previous compressed air setup, with Sonic being even more efficient than the clean dry nitrogen they were considering. The new Sonic system reduced operational costs and eliminated the need for a second backup central compressor. Furthermore, Sonic's solution met the manufacturer's worker safety requirements by operating at a maximum sound level of 80 dbA. The partnership between the manufacturer and Sonic Air Systems has continued for over 15 years, demonstrating Sonic's solutions' long-term reliability and effectiveness.
Related Products
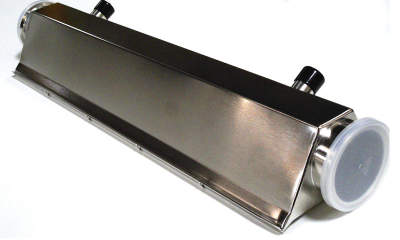
Sanitary Air Knife and E-Z Clean
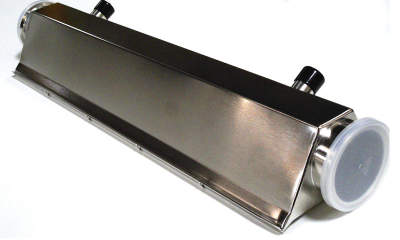
Sanitary Air Knife and E-Z Clean
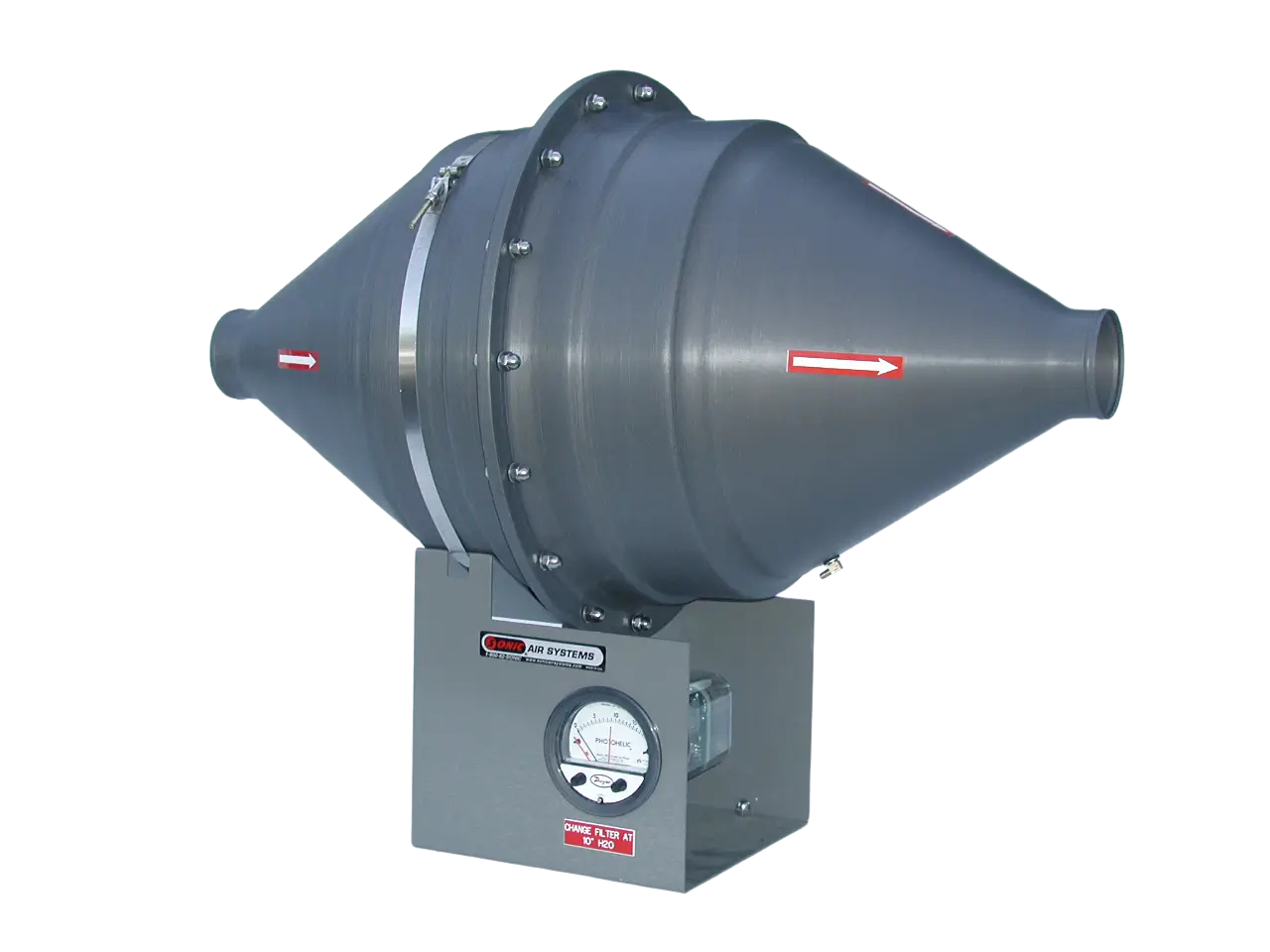
Inline HEPA Filter
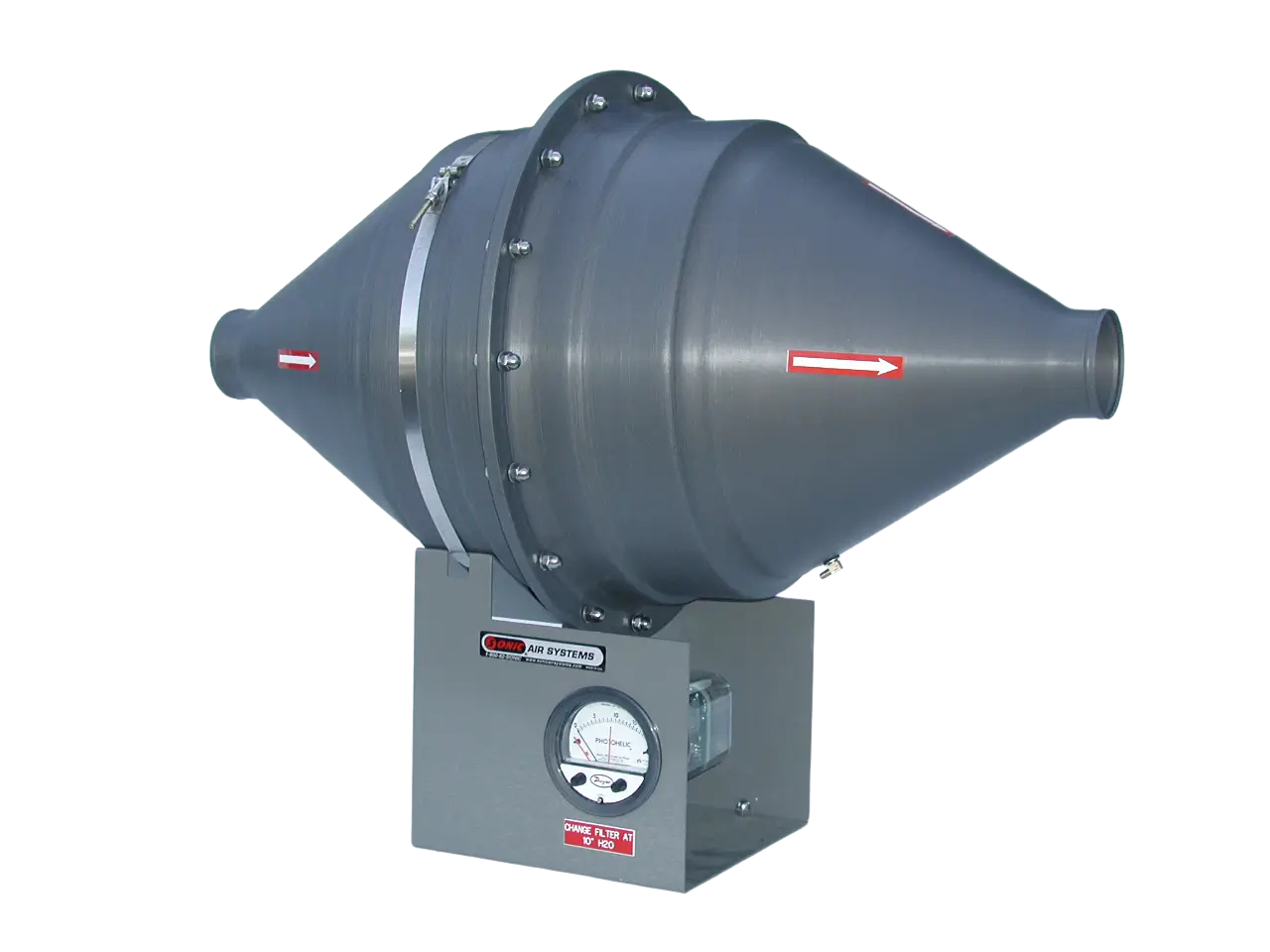
Inline HEPA Filter
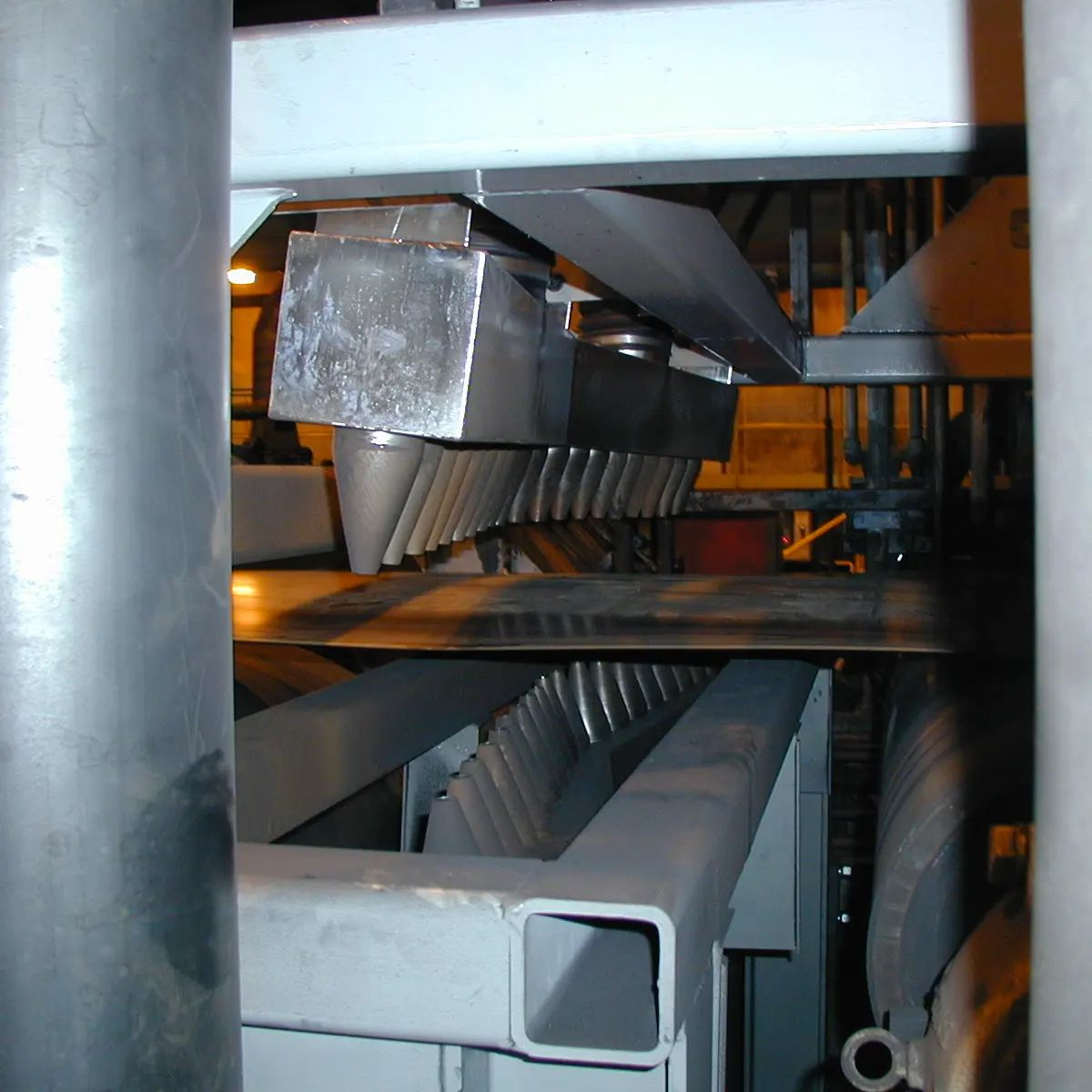