CASE STUDIES
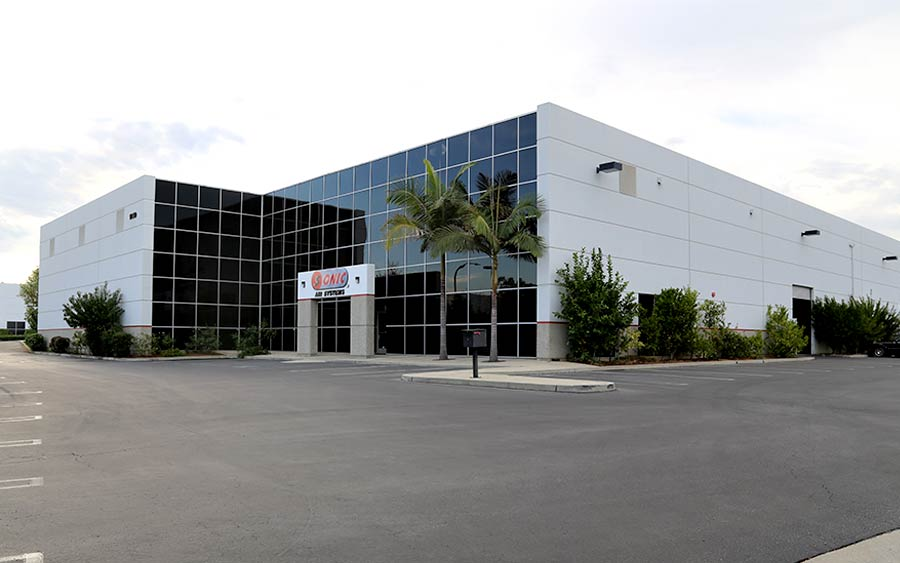
Wire Drying Systems Help Amp Up Capacity in Wire & Cable Production


Overview
The demand for insulated and jacketed wire and cable in the US is increasing, driven by factors such as increased home construction, upgrades in fiber optic infrastructure, EV charging stations, and investments in smart electric grids. During manufacturing, communication to building wires all the way up to large gauge high-voltage trunk cables and complete drying following the extrusion water quenching through is critical.
Solution
Sonic Air Systems is a leading provider of blower-powered air wipe drying solutions to the Wire and Cable industry, with over 30 years of experience. We design and manufacture custom drying tunnels for wires that address the challenges of drying various wire types, coatings, and cables at high speeds.
Our wire & cable drying systems utilize enclosed drying cabinets to contain sound and moisture with automated doors, which also enhances each factory's potable water conservation efforts. We offer a one-size-fits-all drying tunnel for wires that can handle a wide range of diameters, from 0.05" to 4" (1.27-101.6mm) diameter for low-energy airwipes.
Sonic wire and cable air wipes are designed to achieve 360˚ air drying coverage with small & short footprints. We also address challenges such as uniform coverage, noise reduction, knots, and maintenance with our innovative technologies and high-impact air velocity.
Result
Sonic Air engineers low-energy wire and cable drying systems that can adapt to wire and fiber optic cable diameters, eliminating the need to replace drying equipment when production changes cable sizes. This one-size-fits-all approach streamlines operations, reduces downtime, and ensures efficient drying regardless of cable size, speed, or operating conditions.
Related Products
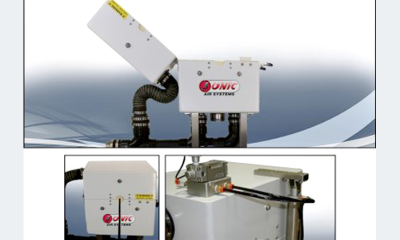
Air Wipe and Wire Dryer
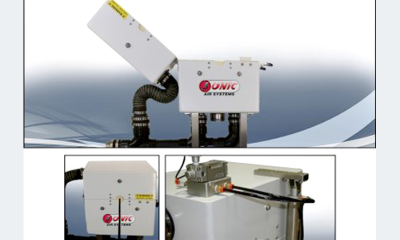
Air Wipe and Wire Dryer
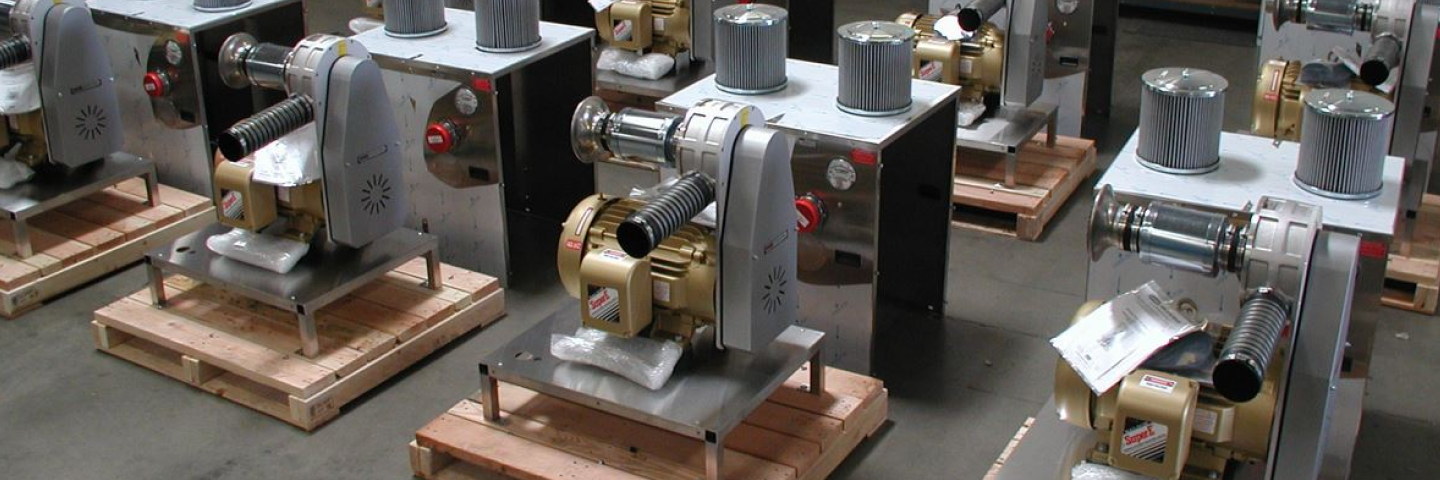
Centrifugal Blowers and Models
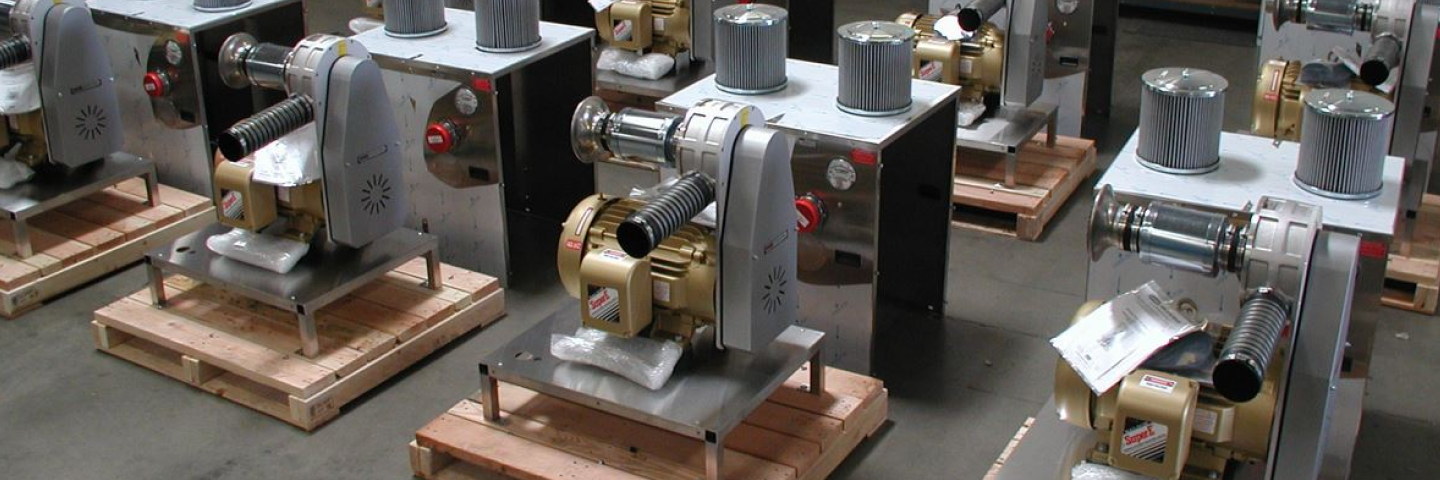
Centrifugal Blowers and Models
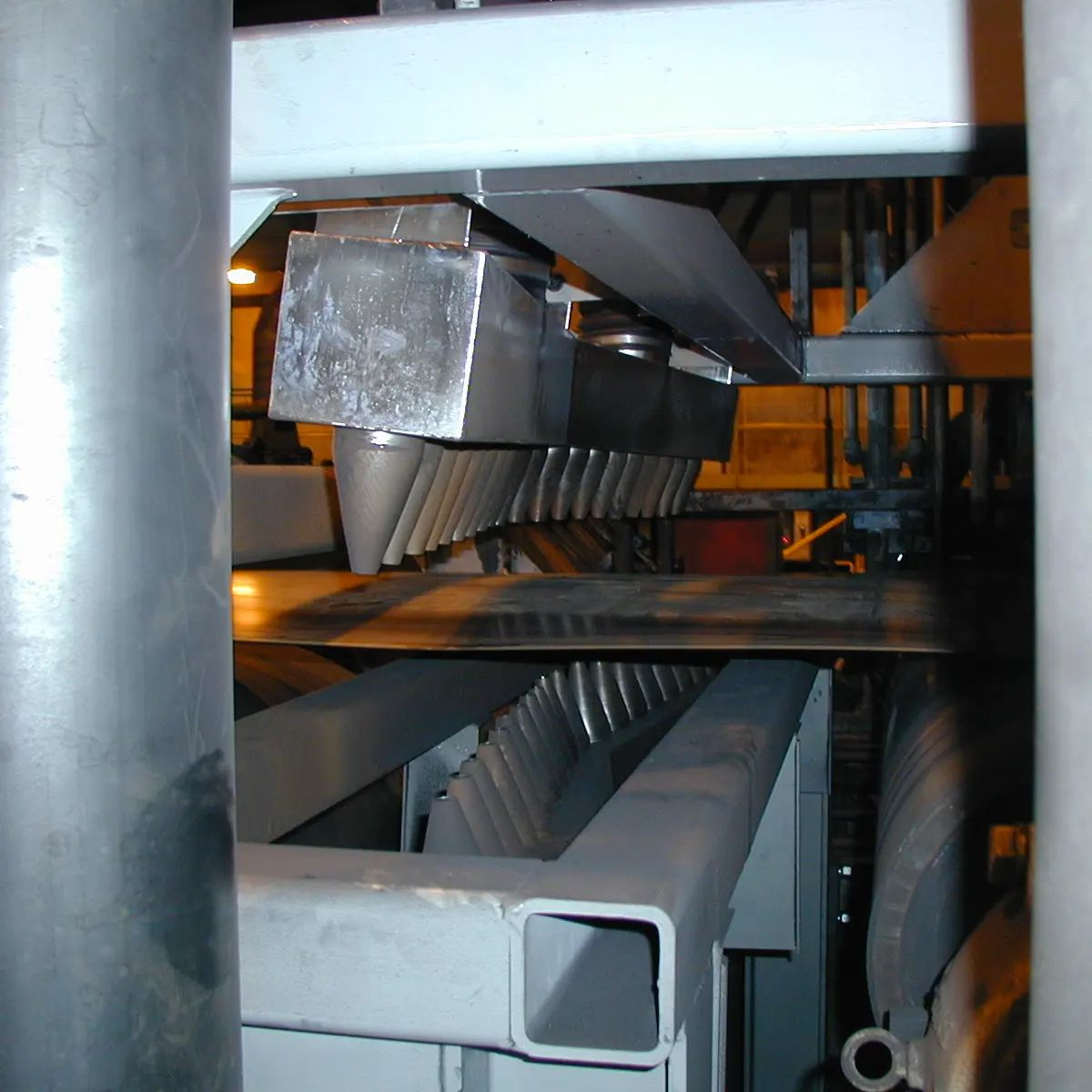