CASE STUDIES
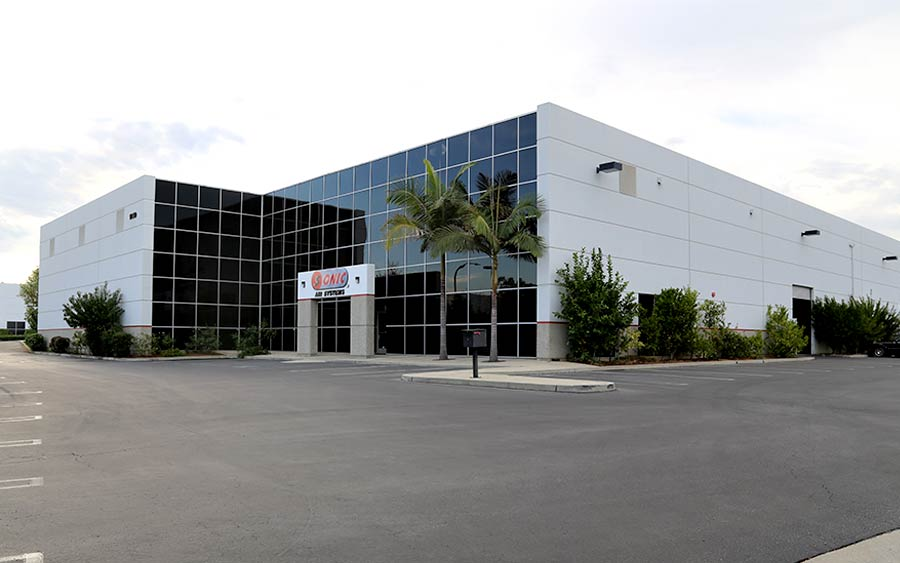
Sonic Compounds Success with Plastic Strand Dyer up to 200 FPM
.png)
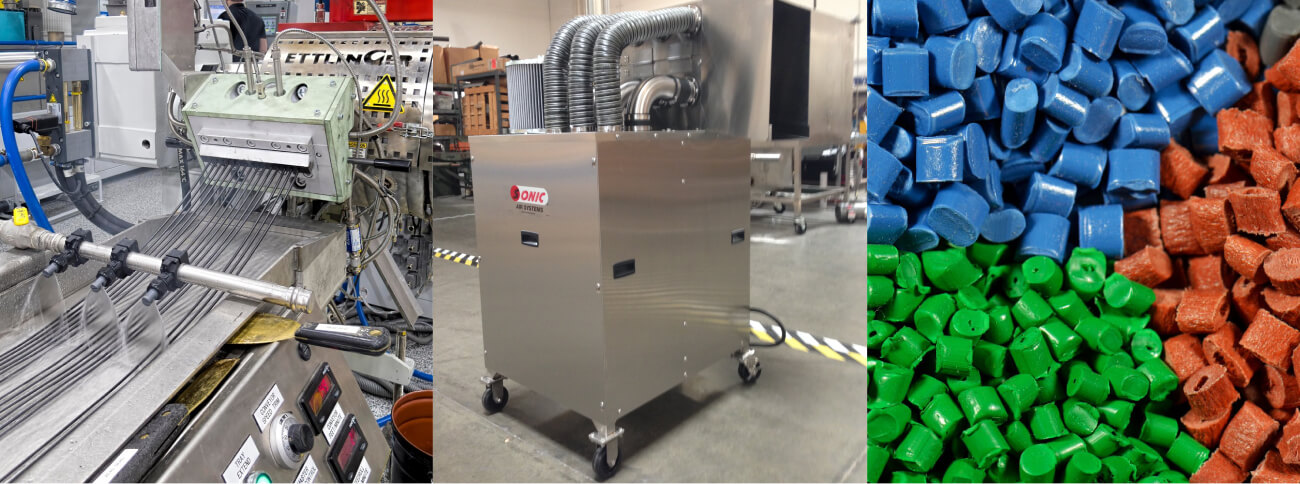
Overview
Multibase Copley, a manufacturer of base material PVC pellets in Ohio, was using two pre-existing blowers and compressed air to dry its plastic strands. Pellets enter a reactor and, subsequently, an extruder, where they are transformed into plastic strands measuring no more than 0.125” (3 mm) in diameter and arranged in no more than 10 rows, with a maximum width of 6” (150 mm). These dry plastic strands are submerged in a water cooling bath, exit at a production rate of 200 FPM (30 MPM), and dried. However, this method was not effective in removing all of the moisture from the strands, causing problems with the quality of the final product.
Solution
Sonic designed a custom, portable plastic strand dryer for Multibase Copley. The plastic profile dryer is powered by a Sonic Blower with Air Knives, which uses high-velocity air to break the surface tension of water films and shearwater off at high speeds.
Result
With Sonic's engineered drying solution, Multibase was able to significantly reduce its production energy costs and achieve its quality and drying objectives. The new compound strand dryer was able to remove all of the moisture from the plastic strands, which resulted in a higher-quality PVC pellet.
Related Products
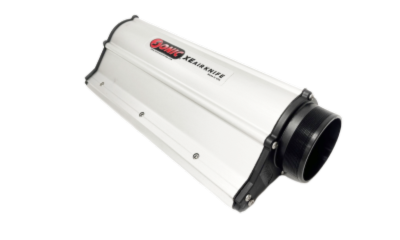
Sonic XE Air Knife
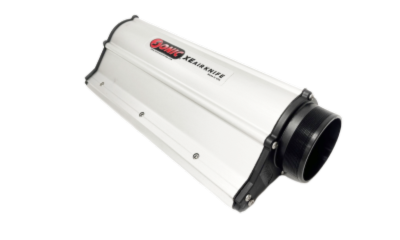
Sonic XE Air Knife
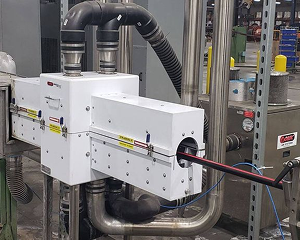
Air Wipe and Wire Dryer
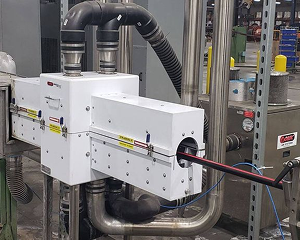
Air Wipe and Wire Dryer
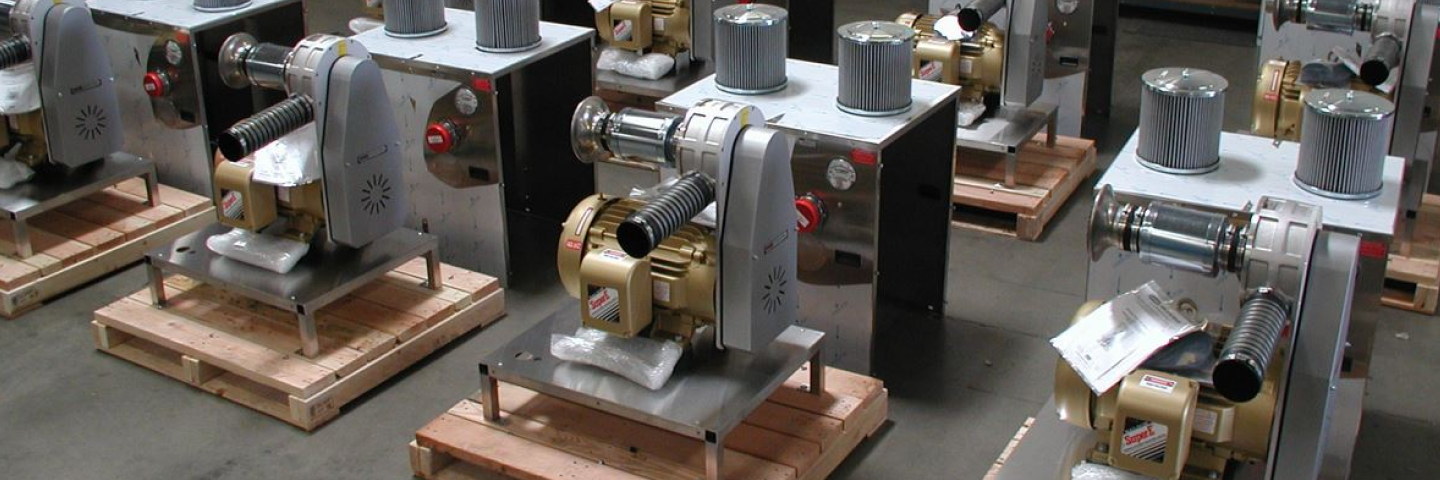
Centrifugal Blowers and Models
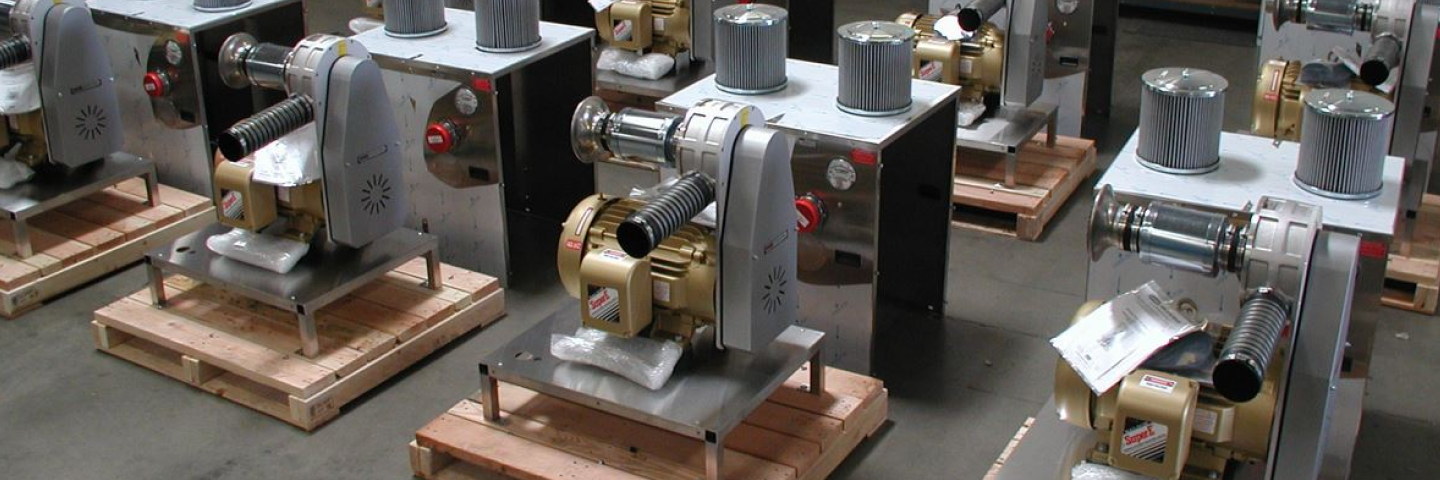
Centrifugal Blowers and Models
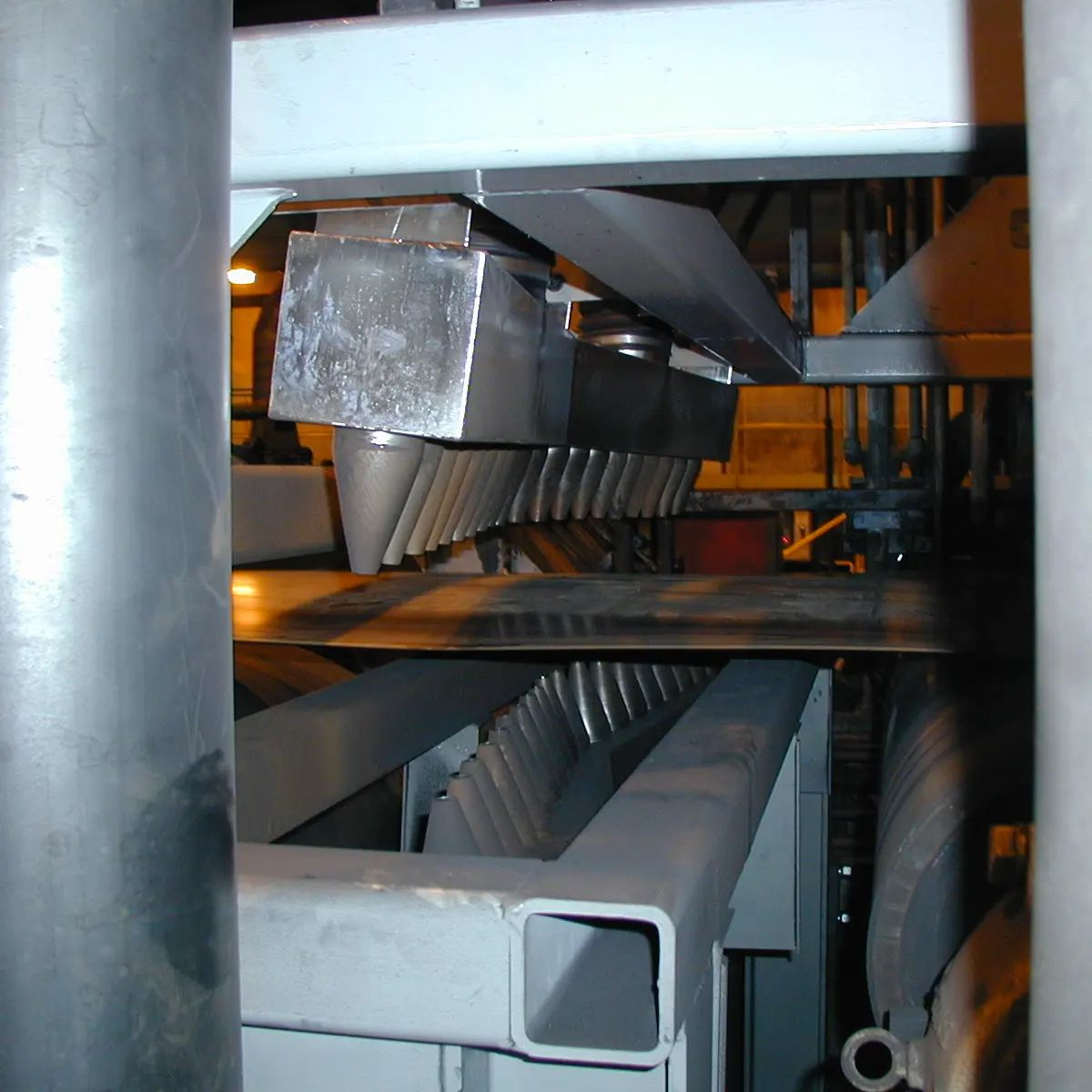